Concrete’s Ways
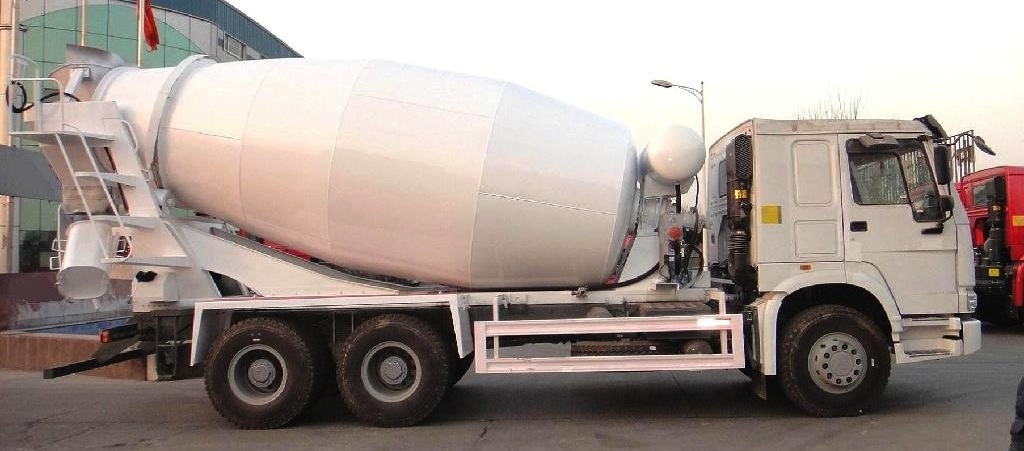
Many times in the past 15 years, articles published by WaterShapes have referred to water as “the main ingredient” when it comes to pools, spas, fountains, ponds and all of the other forms of contained, controlled water. I’m willing to accept that assertion and have probably offered it myself a time or two.
Here, however, I want to make a case for looking at concrete as water’s equal partner in our work. After all, where would “watershapes” be without both the water and the material so many custom designers and builders use in shaping it?
The thing about concrete is that not as many watershapers – even contractors – are as familiar with it and its performance as they are with water and what it can do. It’s been my observation that too many of us see the concrete that shows up on job sites as a commodity and, too often, simply assume that it is therefore consistent, reliable and trustworthy. That’s largely true, thank goodness, but I’ve found that knowing a bit about what goes into concrete – how it is compounded and processed – goes a long way for me in attaining exactly the consistent, reliable, trustworthy performance I seek.
SUCCESS BY DESIGN
It all starts with mix design – that is, the selection of ingredients that go into putting together a batch of concrete – and with specifications put together by the project’s engineers. If you’re among those who don’t think all that much about the role mix design plays in producing concrete of the desired strength and performance characteristics, it’s time to change your ways – and here’s why.
In any quality watershaping project, the engineers will have specified a minimum concrete strength in the documentation. That’s fine, but quality watershapers tend to move well past minimums – and there’s nothing to prevent the contractor (or even the owner) from wanting to use a stronger mix. Helpfully, the added cost here is negligible – and the resulting improvements in performance can be both beneficial and significant.
Concrete batch plants are where discussions (and decisions) about what goes into the material that will be delivered to the job site take place. It’s important to be able to converse with the mix master knowledgeably enough that you (and your engineers) keep control of what’s included in the batch. (Photo by kozmoat | iStock.com) |
In practical terms, setting a strength level requires the contractor to communicate clearly with the “mix master” at the batch plant when the concrete is ordered. It’s a broad-ranging conversation about much more than desired strength: It also includes discussions of weather forecasts, traffic conditions, site access and parking, anticipated rates of placement (as yards per hour), the distance from the truck to the application site and the pumping equipment.
At this point, the mix master will introduce bits of concrete chemistry into the discussion – and this is where the contractor’s knowledge and experience come into play. If you don’t know your way around such topics as air entrainment, water reducers, plasticizers, set retarders and set accelerators, it will be the mix master who has control of the outcome rather than you! And it’s not all just about concrete chemistry, either: You also need to make certain the mix master uses the largest aggregate allowed by the project engineers: The bigger it is, the stronger the concrete will be.
IT’S THE WATER
Your negotiations with the mix master are obviously crucial to the success of the project, so it’s important to get everything squared away at the batch plant. What you’ll learn from experience is that water is the main factor to focus on, because concrete can be significantly weakened if excess water is used.
If that seems a bit picky to you, consider that when water evaporates from concrete, it leaves behind a matrix of voids that, under magnification, look like tiny honeycombs. Not only do these voids create weak spots in the concrete, but they also allow groundwater or rain or irrigation water to penetrate the concrete. This can result in corrosion of the reinforcing steel and will eventually result in project failure.
Adding to the Mix It’s safe to say that we all want the concrete we apply in our projects to be dense and durable – that is, to be a high-strength product. Without getting too deep in concrete chemistry, this is achieved by “tightening” the concrete matrix. The key here is to use plenty of cement, which is the “glue” that holds the concrete together. Typically, for example, we’ll use a six-sack mix where a four-sack mix might hit the specified minimum. A sack is 94 pounds of cement powder – about a cubic foot. It’s an inexpensive addition that can make a big difference. But there’s more you can do to increase concrete’s strength – some standing alone and others generally used in combination: • Reduce the water content Some of the additives listed above are not compatible with others (for instance, fly ash does not go well with some waterproof admixes), so do your homework, ask questions and be certain to read and follow labeled instructions! — P.B. |
The basic point here is that only the amount of water needed to hydrate the cement particles should be used. That’s why the mix master adds water reducers and plasticizers to manipulate the “slump” or liquidity of the mix: These materials effectively stretch the water, and the resulting increase in strength will be significant while at the same time it will result in concrete that stays liquid, workable and pumpable.
A good batch plant knows all of this, and some will even go so far as to know the moisture content of their sand and aggregates and will reduce water volume in the mix accordingly.
A load tag comes along with the delivery truck and includes an assay of the hopper’s contents as well as information on the time at which the material was loaded and the starting point for the counter on the truck’s rotating drum. Some ready-mix suppliers (including mine) also provide an assay of the aggregate in their mix, indicating the compressive strength of the rocks in the mix as a pounds-per-square-inch value.
.
This last point is important, because it makes no sense to apply concrete that contains rocks weaker than your compression objective. This can be a big issue if, for example, your mix supplier uses a weak, inferior material (such as quartz) as the aggregate. If your mix master doesn’t volunteer this information, ask: He or she is required by building codes to tell you!
ON-SITE DETAILS
So the order is placed, the mix designed, the trucks loaded and the site prepared for concrete delivery. Now it’s time to focus on what can happen during the application process.
As contractors, it’s our responsibility to ensure, once the trucks arrive on site, that the mix design is not adulterated or altered in any way by “well-meaning’ individuals. Concrete pump operators and ready-mix truck drivers often require some policing: When a truck arrives, quite frequently the pump operator will tell the driver to add water to the mix. Don’t let this happen! Before the concrete is even out of the truck, its strength will be compromised!
(You don’t have to be close by to know when this water addition is happening: After the truck arrives, if you hear the engine revving and the drum spinning rapidly, it’s a tell-tale sign that someone is, for whatever reason, adding and mixing in additional water.)
If you see something like this happening before a concrete batch has been pumped over to your watershape, don’t hesitate to get involved, because adding excess water to the mix can seriously compromise the concrete’s strength. (Photo by VanWyckExpress | iStock.com) |
It’s also very important to communicate with the batch plant about a delivery schedule and do what it takes to make certain a load doesn’t sit too long in a truck, waiting to be pumped. The result may be that the concrete will set in the drum, which would ruin the load and might even damage the truck and pumping rig. Using set retarders in the mix can give you more time, but it’s important nonetheless to develop a sense on site that everything has to go like clockwork to ensure success.
This is where the truck’s rotation counter comes into play. The concrete’s components are added dry at the batch plant; once the specified amount of water is added, the rotation of the drum and its vanes actually mixes the concrete. Ideally, once mixing is complete, the drum should turn as few times as possible before its contents are removed and applied.
If it’s being pumped into tall forms (such as tall walls or caissons or deep footings), the concrete must be applied from the bottom up rather than dropped in at the top and allowed to fall to the bottom. The fall separates the aggregate from the mix and compromises the concrete’s strength. It can also create large, undesirable voids and air pockets in the finished matrix.
In these cases, proper consolidation must be assured either by having the right mix design for the application or by vibrating the material once it’s been applied. But there are limits: Excessive vibration may cause the aggregate to settle to the bottom!
SEEKING A CURE
Once applied, concrete does not “dry”: It cures. As water fully hydrates the components of the concrete mix, crystalline structures form that give the concrete its density. This is why controlling the rate of water evaporation is so important: The goal is to have the water leave the concrete as slowly as possible – that is, for it to cure properly.
[ ] Covering the newly applied surfaces with burlap, carpet or plastic is the most rudimentary of curing aids, but those materials are not recommended because they can cause discoloration by trapping moisture at the surface. They are also susceptible to being moved or blown out of position.You don’t have to have encyclopedic knowledge about concrete chemistry and technology, but it’s important to know enough that you, as a contractor, have enough information at hand to know you’re getting the results you want. After all, do you really want to face the possibility of having to start all over again? |
But take care and get the right chemical! Some curing aids produce a “bond breaker” that inhibits the bonding of subsequent surfaces, meaning plaster or stonework may not adhere to the concrete. Why do such products exist? It’s because they’re useful in curing roadways, bridges, sidewalks and other high-traffic surfaces. And they’re typically easy to avoid, because they are more expensive than the appropriate alternatives.
MAKING SENSE
It’s often said that failure is the best teacher, but in the case of watershapes, taking chances with concrete shells meant to contain large volumes of water is not a comfortable classroom. The expense involved in correcting errors or dealing with failures is often enough to break a business. Even if that’s not a consequence, the time, energy and expense involved in returning to the site and doing things the right way is a massive exercise of going backwards.
This is why all watershapers (and especially watershape contractors) who work with concrete need to come to the table with certain knowledge of the material and the application process in mind. Concrete chemistry can be a lifetime’s study, but for typical watershapes, it’s not rocket science by any means. Still, there’s enough at stake that it’s best to be prepared: Achieving strong concrete is complicated enough that it requires care and attention with each and every project.
Paolo Benedetti is principal at Aquatic Technology Pool & Spa, a design/build firm based in Morgan Hill, Calif. He may be reached at paolob@aquatictechnology.com.