Considering Service
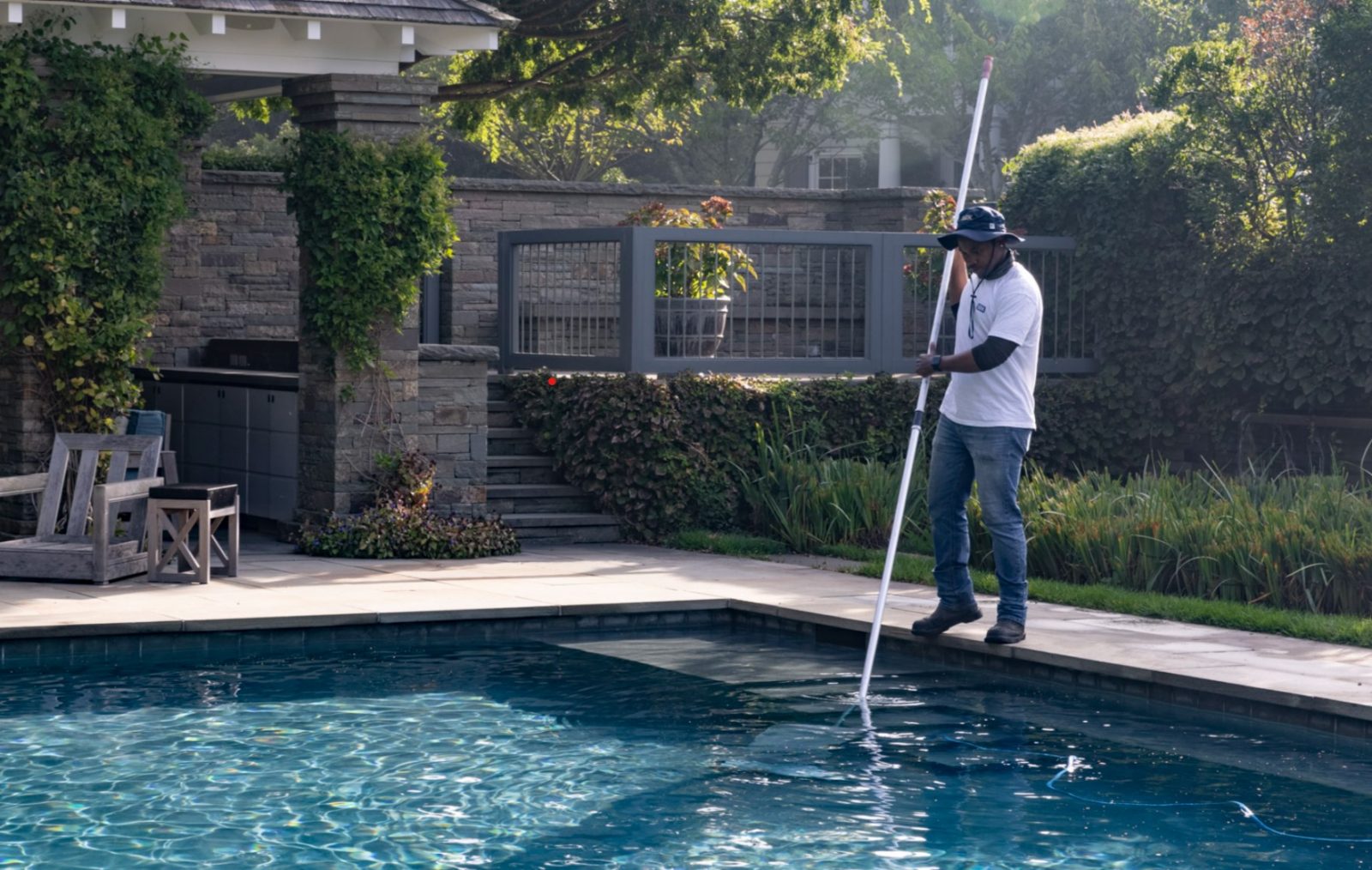

All watershapes require service and maintenance. How easy or difficult the needed maintenance tasks are for the service technician is largely due to decisions made by the build. Here Steve Kenny explains how his years of service experience, and running a service division, influence his company’s approach to engineering and construction.
By Steve Kenny
Like many pool builders, I started out in the industry working on a service route. I went to work for my family’s company more than three decades ago after a stint as a chef in New York. I quickly learned that servicing pools can be incredibly demanding, physically and mentally. Unlike working in the kitchen of a five-star restaurant where the environment is completely controlled, pool service is all about responding to a spectrum of constantly shifting circumstances and conditions.
It’s true that no two watershapes are alike but it became painfully obvious to me early on that many, if not most, are not created to maximize serviceability. From poor circulation to inadequate chemical treatment, improper filtration, and a host of other factors, the hand dealt to servicers is often largely problematic.
That broad range of wasteful disconnects was the main reason I decided to start building pools. I knew there had to be a better way — one that would ease the service burden and ultimately result in lower operating costs, far less downtime, and better water quality for consumers.
It’s been a long road to perfecting pools built with serviceability in mind. It is one that has led to a number of lessons and, I dare say, revelations that I believe can and should be embraced by the entire watershape construction industry.
Here are some of the practical measures our company has embraced.
ALL TOGETHER
The first and most important concept is that serviceability does not rely on any single factor. It’s a combination of synergistic elements that work together to create a body of water that functions reliably under changing conditions.
It’s not just about efficient circulation, resilient chemical treatment, effective filtration, proper skimming action and efficient equipment layout – but all of those elements, and more. There is no single solution, but instead a collage of measures that work to enhance the function of all the others.
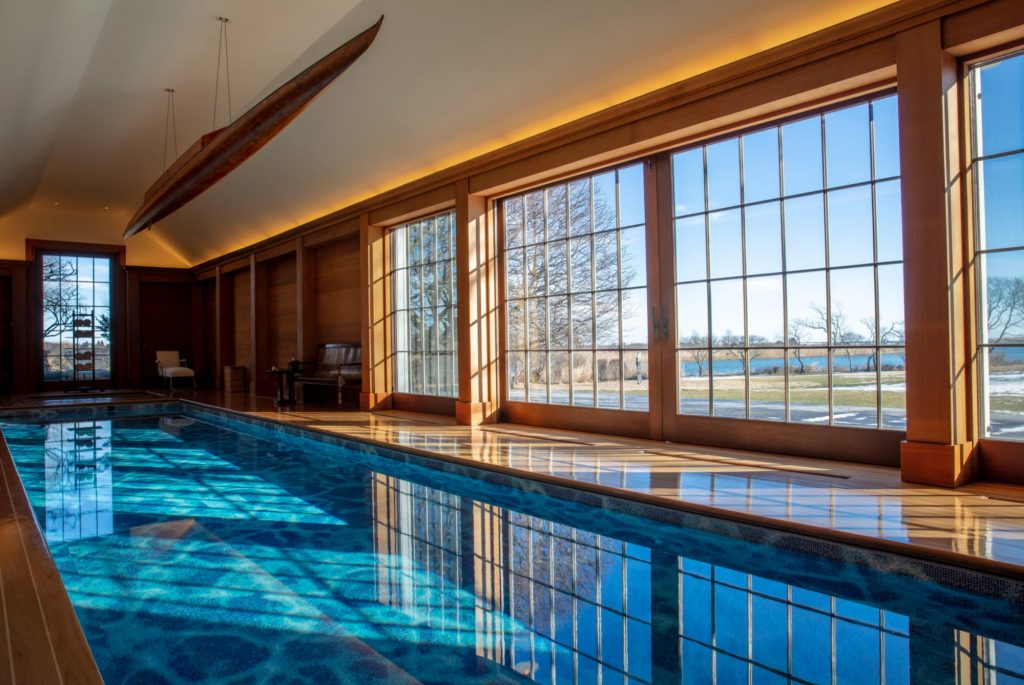
These days, the pools we build combine both beautiful aesthetic design, and equally elegant functionality. Yes, there are new technologies that can be a big help, and some of them are very expensive. But truth be told, every pool can be built to maximize serviceability and user satisfaction.
Frankly, I moved into construction because I grew tired of maintaining other builders’ interpretations of a “good pool.” The pools that we’ve built are easy Our service techs experience it on a daily basis.. The water is always clear, regardless of bather load and environmental conditions, and the systems are easily accessible.
By contrast, pools we service that were built by others are where we constantly run into problems. When the filtration, chemistry and other factors can’t keep up with changing conditions, there are always challenges, usually manifesting in problems with algae and cloudy water.
This is true both for residential and commercial pools, high-use pools and those that are rarely used for swimming. In clear contrast, pools built for service consistently exceed consumer expectations and experience unexpected problems far, far less frequently. Serviceability and reliability go hand in hand.
Of course, it’s important to note that there is no such thing as a service-free pool, but when you follow a handful of basic principles, you can come close, vastly increasing service efficiency and reducing worker fatigue. Our goal is to build a package so that the client doesn’t struggle and our service techs don’t struggle. When we do that, everybody wins. Let’s break it down here:
FILTRATION
This is probably the most controversial point on this list. I am not a fan of micro-filtration, meaning DE or cartridge filters, and instead prefer sand, both from a serviceability and water-quality standpoint.
I certainly understand why people turn to DE and cartridge filters. By filtering to small micron sizes, they are able to generate beautifully clear water, at least at first. Experience has taught me that when these filters load up, they reach a point of diminishing returns and water quality can actually suffer. The answer to that is, of course, to routinely clean the filter elements.
Anyone who’s worked a service route with DE and cartridge filters knows what a time-consuming pain it is to clean a DE filter and dispose of the used DE. And they know that removing, cleaning and replacing filter cartridges is equally burdensome. Yes, many companies rely on these procedures to generate revenue, but that’s not our business plan.

I like the reliability and ease of maintenance of sand filtration. The only routine maintenance is backwashing, which can be done automatically. In terms of raw labor, there is no comparison. (We’ve also had great success with activated glass sand replacements, which supplement sanitizing and oxidizing capacity.)
As for water quality, when you have a system with proper circulation, skimming action and chemical treatment, sand filters are more than able to sustain clear water.
With that said, let’s turn to some concepts that are entirely undebatable.
CIRCULATION
Water flowing through pipes in a watershape is equivalent to circulation in the human body. It effects everything.
When we build a pool, circulation is entirely synergistic. We look at the flow rates, the turnover rates, pipe sizing, the pump curves, filter size, the flow requirement for the heater. We also try to eliminate dead spots in the pool by distributing return fittings so that the entire pool is treated chemically.
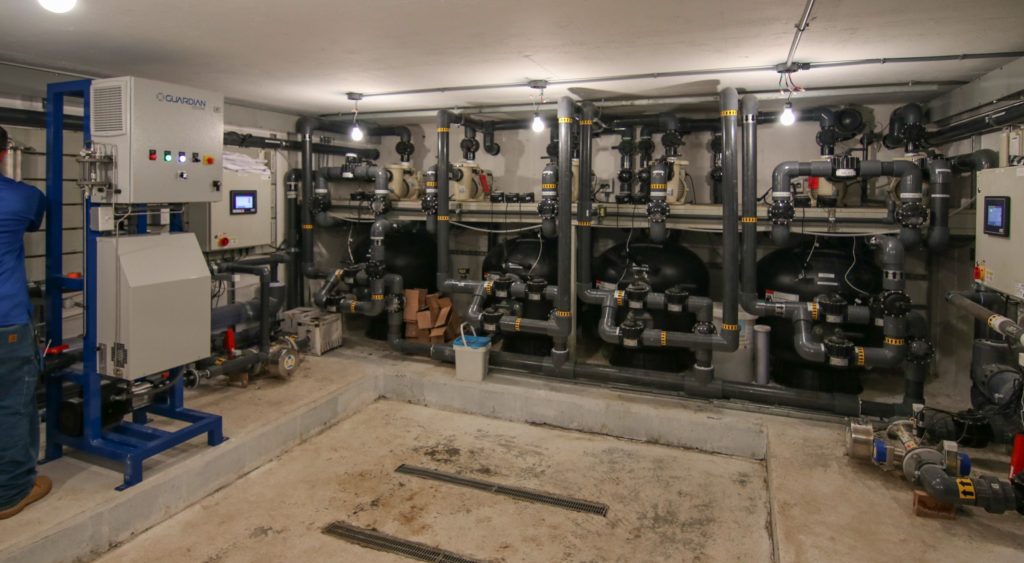
Dead spots lead to algae and places where dirt and grim can collect, and they promote algae growth. (I’ve found that pools with returns in the floor are extremely easy to clean.)
And we always make sure we have adequate skimming action. It’s critical to have enough skimmers – and one is never enough and two is the bare minimum on a small pool – so that you’re always removing that top layer of water, which contains the vast majority of dirt and debris.
You always want to see that skimmer weir flapping, capturing the floating debris before it sinks to the bottom. When that material is allowed to sink, cleaning the pool becomes far more labor intensive.
VAULTS & PADS
This is a huge point, and a constant battle servicing many pools – inadequate space for equipment, poor access and inefficient layout.
Here in the northeast, we have a lot of inground equipment vaults and so often they have a small hatch and a ladder, which make simply getting in and out of the vault difficult, let alone moving equipment and materials.
It’s a fact of human nature, we avert difficult and unpleasant tasks whenever possible. When it’s a pain to access the equipment area, there are service techs who will put off some tasks because crawling to a cramped, hot and smelly bunker with no lighting and spiders is more than they can stand sometimes.
When we build pools, we insist on adequate space and accessibility. We calculate the space required and plan the equipment layout, trying to keep it as simple as possible. Our equipment rooms are well-lit and well-ventilated. And, whenever possible, we build steps leading to subgrade vaults with standard-size doors, so a human can actually get in and out with ease.
Designing the equipment layout is a huge subject unto itself. Here I’ll say that we apply logic, geometry and planning, so that it’s easy to first understand how water flows through the equipment set, and so the technician can access all the pieces he or she needs to touch, frequently or infrequently.
I’m not a big fan of tandem systems and shared equipment for the pool and spa, or associated water features, because it complicates the layout, which leads to mistakes, especially by inexperienced technicians. You don’t want technicians having to think too hard about how to set valve actuators so that they don’t accidently drain the pool or overflow the spa. It needs to be obvious.
I understand the economy of shared systems, but it’s always better in my opinion to dedicate equipment to a specific function because it makes it far easier on the servicer and minimizes mistakes.
CHEMICAL TREATMENT
There are many ways to chemically treat a pool, and I’ve worked with them all, or close to it. For many years now, I’ve been a huge proponent of taking chemical treatment systems to the next level and have written about it numerous times. We’ve worked to position our systems as the best available.

It’s really a system within a system that ultimately supports superior water quality and ease of service. (insert link) I advocate for CO2 injection systems, and we always take care to make sure it actually works, often adding a static mixer after the injection point. Automatically controlling pH and alkalinity prevents a range of issues and it greatly simplifies maintaining balanced water.
We use a combination of UV and ozone on a bypass to provide the heavy lifting for sanitization and oxidizer demand. And we inject small amounts of chlorine to provide a constant and low residual.
We still build systems using chlorine-only, again, always looking at the entire system. When the filter is sized correctly and the all-important skimmers work, the water is balanced, as described above, all-chlorine pools can become very easy to service and able to sustain quality water that doesn’t smell.
ADDITIONAL ASPECTS
Saltwater chlorine generation: Another vast and often controversial topic, having worked with numerous salt systems, I do not recommend going that direction with my clients, due largely to issues with water balance and corrosion.
Covers: Purely from a service aspect, solid safety covers have pros and cons. They do keep the water cleaner, and blocking the UV rays slows down chlorine degradation. They can be a pain to clean, however, because they do collect debris and water.
Still, they reduce evaporation, retain heat and most importantly, prevent drowning incidents. In the case of covers, those advantages will often drive the decision for the client.
Pitched decking: It sounds like such a simple thing, but it’s crucial to make sure the decks are pitched away from the pool. Rainwater runoff from decks and surrounding landscape will cause a litany of heartaches for the service technician.
Autofill systems: Another no brainer, auto-fills sustain the water level and remove the need for the servicer to manually add water. The simple mistake of forgetting to turn off the hose can lead to disaster if the yard or worse the house floods.
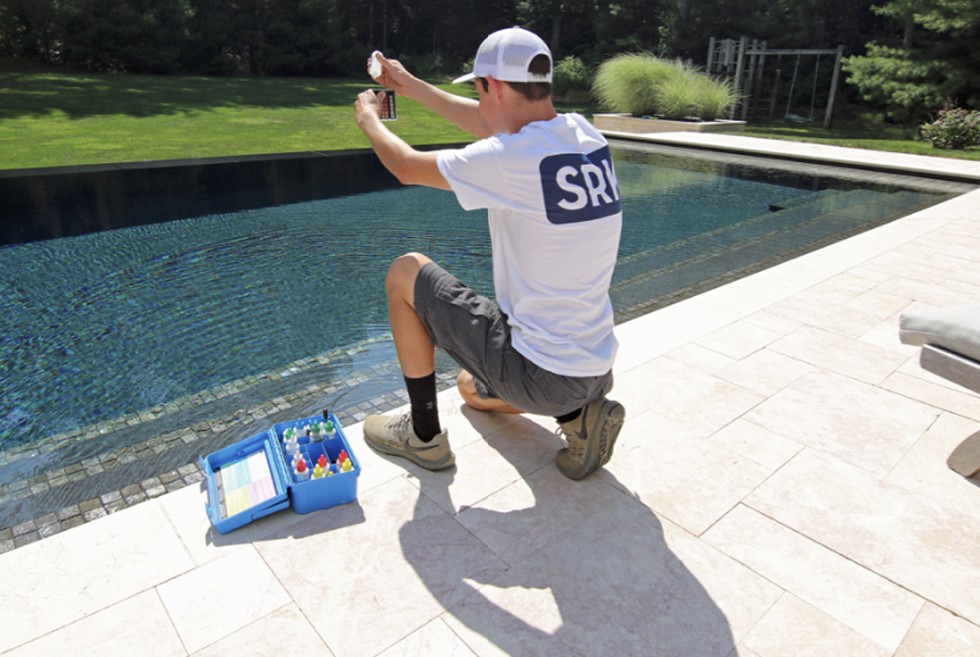
Overflow lines: Mother nature can also flood a pool, creating the same kind of potential problems, and a nightmare for the pool service guy who shows up to find water flowing over the coping. All pools should have an overflow.
Interior surfaces: Although largely an aesthetic choice, there’s no question that some surfaces are more problematic than others from a service perspective. I recommend polished-aggregate surfaces. They look great and sustain their appearance more reliably than traditional plaster.
SYSTEMS VALUE
I believe when we fully consider the question: “Would I want to maintain this pool?” it leads to decision-making that dramatically eases maintenance, and elevates the entire pool-ownership experience. It also doesn’t drive people way from pool service work. Many will quit if they get sick of the unnecessary hassle and frustration. From a business standpoint, the service tech’s time is better spent maintaining quality systems.
Yes, it requires budget and cooperation from the homeowner and often others on a project team. I describe and advocate with the idea that it’s an investment in a positive experience for everyone involved. Building for service implies a standard of care that leads to resilient pool systems, happy service technicians, and satisfied customers.
Steve Kenny is an aquatic designer, builder and technician with more than 30 years of industry experience. He owns and operates SRK Pool Services, a high-end construction and service firm on Long Island, New York, and consults on projects near and far.
This article first appeared in WaterShapes in August, 2022.