Indoor Fortitude
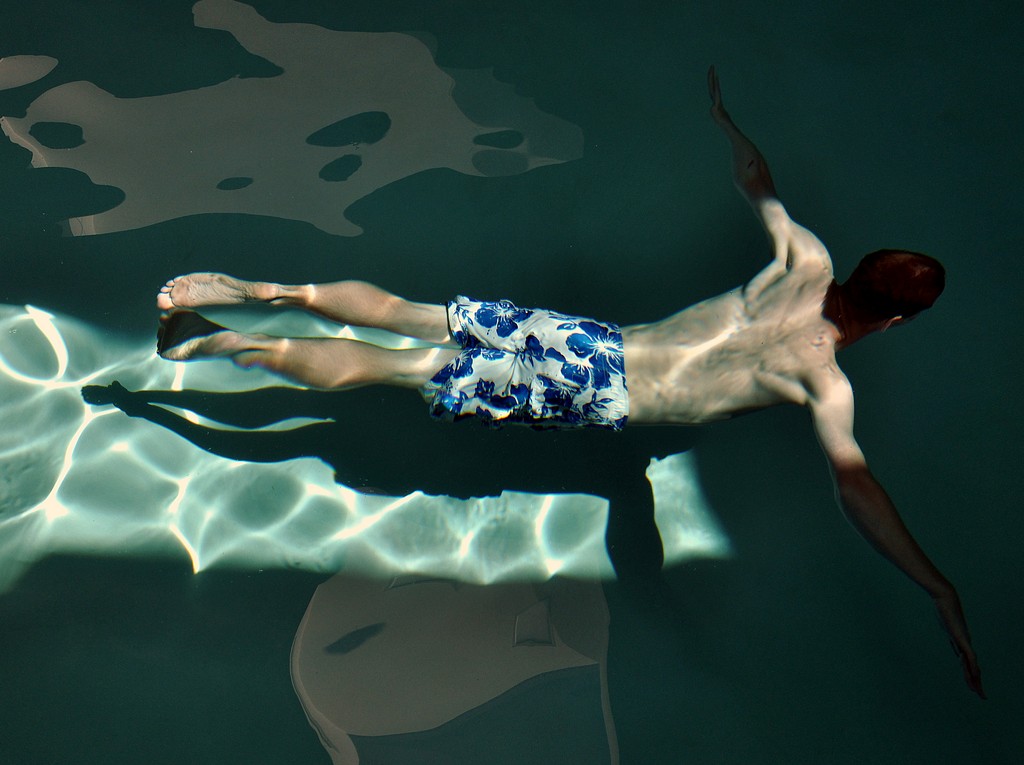
By William Drakeley & Jeffrey Boucher
For professionals who tirelessly commit themselves to excellence in all aspects of their work, challenging projects are the butter on the bread.
At Drakeley Swimming Pool Co. of Bethlehem, Conn., we truly enjoy jobs with higher-than-usual degrees of difficulty because they generally involve us with clients who have strong ideas about what they want, force us to develop solutions to unique and interesting problems and see us perform on a level that invariably makes us proud. As we see it, these jobs are the reward we get for years of focusing on doing our absolute best.
True, these projects can be tough, but we’ve found that by sticking to our “quality without compromise” philosophy, we’ve managed to thrive through tough times and have always earned our share of interesting commissions. It’s proof of the old adage that good things follow hard work, even in a soft economy.
That was certainly the case for the job discussed here and in the July/August edition of WaterShapes, where, in “Inside Maneuvers” (page 42), our colleague Kevin Ruddy described the design work he and his company did in what turned out to be a three-and-a-half-year construction project for our firm. Here, in this follow-up article, we’ll describe an installation process that forced us to perform at the absolute top of our game.
A GRAND SETTING
The residence in question is decidedly upscale, situated in a rural, forested area of Connecticut known for beautiful homes inspired by the great turn-of-the-20th-Century architect Ehrick Kensett Rossiter. As part of an elaborate renovation, the homeowners had retained Kevin Ruddy of Omega Pool Structures (Toms River, N.J.) to design a new indoor pool.
We had worked previously with the general contractor on a few high-end homes in the area and ultimately were brought in as one of two bidders to install a pool that was to form the home’s new wing. We knew Ruddy’s reputation and that he was a member of Genesis 3, but we’d never worked with him before. His plans really told us all we needed to know: We were immediately impressed by both the precision and level of detail in his design.
That was significant, because as a rule we’re not generally thrilled to work with “swimming pool consultants.” Far too often, we’ve found them to be less than fully competent when it comes to developing anything more than a vision we’re then challenged to execute more or less on our own – basically in high-wire acts without nets!
To ensure the shell’s long-term reliability in its indoor setting, we made it with 12-inch-thick walls on a double curtain of #4 reinforcing bars on six-inch centers – more than adequate to carry the watershape through any future remodelings of the surrounding structure that might come along. For further durability, we shot the shell as a monolith with no expansion or cold joints, aiming for a compression strength of 5,000 to 6,000 pounds per square inch. |
In this case, however, we were enthusiastic about Ruddy’s contribution from beginning to end – pleased by his depth of knowledge of indoor pool design and engineering and especially happy with his approach to writing specifications, which were all about defining performance rather than pushing us to work with specific pieces of equipment noted by make and model.
As we see it, we know enough about completing elaborate residential and commercial pool systems that we don’t need that kind of help, so his approach and ours were a perfect fit.
Indeed, by leaving equipment selection up to us, Ruddy gave our team the freedom to choose components that we’ve used and know inside out. We’re not only familiar with performance characteristics, but also know all about where to get what we need; the availability of technical support; and what it takes to troubleshoot incidental issues that might arise. In essence, this assures us that the system will operate per specifications from the outset – and will continue to perform as designed because we know the equipment is reliable, durable and serviceable.
We also had the huge plus of having worked on indoor pool systems in the past. Even though this was a residential project, it wasn’t significantly different (other than in scale) from the numerous indoor pools we’ve built for high schools and universities. Basically, it boils down to building a pool inside a big box made of concrete masonry units – a process that brings an unusual set of challenges with it.
TRICKY PLACEMENT
A big component of these sorts of projects has to do with working around other trades.
We knew this going in, so we weren’t in any way surprised that the process involved a number of starts and stops as well as some unusual overlappings of responsibility. The general contractor, for example, was the one who did the rough excavation for the pool before preparing the foundations for the walls of the enclosure.
Only when he was finished did we come on site, lugging or craning in equipment and materials required to build the under-drain system. Then we stopped and waited for our next turn on site, moving onto other projects in the meantime.
That staccato process is all fine so long as everyone involved understands the nature of the work and how the project will unfold. In this case, that unfolding was actually quite smooth, with very few scheduling problems or conflicts. And that was true despite the fact that a number of project elements were quite challenging and brought their own levels of stress to the process.
One of the clients’ strong aesthetic desires was that they did not want to see the leading-edge bar of the retracted automatic cover – an unusual challenge because of the distinctive patterning of the stone deck. To ensure stability of the walking surface above the cover box, we custom-fabricated brackets onto which the individual stones were bolted and ultimately managed to hide the cover completely in a long, narrow slot. |
Consider the building site, for example: Although the soil was generally sound, the pool was being installed perpendicular to a slope. As a result, the shallow end was to be buried three feet below grade, while the deep end would hang about six feet above grade. The subsurface material included pockets of sedimentary ledge, meaning there was a high probability that intermittent subsurface water movement would be a factor.
While it’s important with any pool being built under such conditions to provide for some means of relieving hydrostatic pressure, it’s even more critical with indoor pools because any movement will tend to damage not only the pool but also surrounding deck, the enclosure and sometimes even the foundation of the house itself.
In fact, all it takes is a plumbing leak of some kind nearby (with irrigation systems being the most common offender) to create serious problems. So we take no chances and enter into construction of these pools with the understanding that water will need to be collected from around the base of the pool structure and safely removed.
In this case, once the excavation was complete and we gained site access, we placed an under-drain system consisting of four-inch perforated pipes in the floor to collect water, send it to a trunk line and move it along to a drop-off point well away from the pool in the nearby forest, where the water can percolate harmlessly into the ground.
Our next challenge came in the forming stage. Working indoors – especially in a relatively small space – is always something of an issue, because we maintain such extremely high standards when it comes to achieving dimensions and elevations with solid, non-vibrating forms.
STRAIGHT AND STURDY
In this case, the forms reach all the way to the stone sub-base we placed around and atop the drainage system, and we had to be fairly creative in how we deployed our vertical and horizontal two-by-fours to support the plywood structure. There was lots of outstanding carpentry involved, and it also took our practiced ability to improvise and support everything adequately in confined spaces.
As mentioned above in the context of dewatering, the importance of a sturdy, immovable pool structures cannot be overstated – but it’s of even greater significance in indoor settings, where even the slightest movement can spell disaster for surrounding structures. Moreover, addressing any form of cracking or any other structural deficiencies in the shell is much more difficult when a pool is situated indoors.
With that in mind, our goal with indoor projects is always to set them up in such a way that they will perform reliably and in perpetuity.
That’s why we built this shell with 12-inch thick walls featuring dual curtains of #4, grade-60 rebar on six-inch centers. While that may seem over-engineered, we’ve found in other projects that, somewhere down the road, it’s likely an indoor pool’s walls will be surcharged in some unexpected way as part of a future remodeling.
The clients made it clear that everything had to be just right, so precision was our watchword in this project from the start. This extended to every detail, from the smooth, custom aluminum light rings to the stone skimmer lid and the beautiful waterline tile. |
In addition, we don’t build the surrounding structures, so we can’t be completely assured that all of the stresses on the walls have been calculated and accommodated. And despite the possibility that a pool isn’t intended to serve as a load-bearing footing, the builder nonetheless can be held accountable if there’s a subsequent failure because of added forces. In addition to all of those factors, we also knew in this particular case that these were clients who were known to alter the scope, shape and extent of the project with no notice.
To avoid any problems, we made certain that the pool could function as a structural footing come what may, thereby relieving ourselves of any concern about the future. It’s not that we had specific reason to question the engineering of the work going on around us – far from it. All we wanted to do was assure ourselves that, for most imaginable situations, the shell would be ready to function as part of some larger future structure.
One more point: At the clients’ request, the pool was designed with 90-degree transitions between the walls and the floor – no coves at all. There’s strength in those curving shapes, however, and the thicker-than-usual walls gave us complete confidence that we’d have adequate strength at all floor-to-wall transitions.
We shot the entire shell as a monolith with no expansion or cold joints, aiming for a compression strength of 5,000 to 6,000 pounds per square inch. (At this point, five years after the shoot, we’re confident based on compression tests on past projects that the level is now in the 8,000 psi range.)
This approach extends from the fact that our company is less a pool-construction firm than it is a structural-concrete specialist: We never compromise just because a project is residential rather than commercial or because we don’t anticipate that there will ever be additional stresses placed on the structure. We sometimes lose jobs because our performance standards are unusually high, but we never need to worry about structural failures, either. For us, that’s a worthwhile trade-off.
WORKING WITH THE CLIENTS
Beyond the broad, structural issues highlighted above, this project also engaged us with a number of issues that flowed from the clients’ ideas and aesthetic sensibilities.
One of the trickiest of these arose from the clients’ desire not to be able to see the leading-edge bar of the automatic cover when it was stored in its vault. Normally, that bar is visible, so hiding it left us with the need to engineer a way for it to retract under the coping by several inches and leave nothing for the clients to see other than a long, very narrow slot along one side of the pool.
This wasn’t a huge problem by itself, but it was made somewhat more difficult by the fact that we had to accommodate the deck’s stone pattern without interruption while also making it safe and sturdy enough to walk on as well as easily removable for servicing.
The pattern includes stones that are six and 18 inches wide, so part of the challenge was to figure out a way to keep the six-inch stones from tipping up when anyone stepped on their edges.
The selection of the plaster color became a major conversation (yet to be fully resolved), but we had more practical issues in mind when it came time to apply the interior finish: We had to protect the already-completed interiors from any damage. So even though the pool was indoors, we tented it during the plastering stage and kept the dome in place until the pool was filled. |
After a great deal of discussion and plenty of head scratching, we fabricated a system of angle-iron brackets that directly support the stones. The brackets include vertical strips with holes paired with matching holes we drilled into the stones. This enabled us to bolt all of the short stones in place.
At each decision point, we contacted the cover’s manufacturer, Coverstar of Lindon, Utah, to be certain nothing we were proposing would interfere with the cover’s functioning. As it turns out, our use of the brackets in no way impinged on the cover system or influenced its performance in any way. So now, when we look at the deck over the cover vault, we see zero disruption in the deck’s appearance – just as the clients wished.
Another aesthetic issue had to do with the lights – and more specifically the light rings we usually use. For years, we’ve recommended and used a light that features a ring with what we consider a timeless Greek T pattern and a highly polished finish. The clients weren’t happy on either score, and when we found a product that had just the satin finish they preferred, it turned out that the rings were made with such a poor grade of stainless steel that we couldn’t recommend their use.
After numerous tries, we selected lights supplied by Pentair Water Pool & Spa (Sanford, N.C.) and fitted them with custom light rings made of billeted aluminum. We went with aluminum for two reasons: It had the look the clients wanted and also had the ability to withstand the specific water conditions found in the pool.
IN THE WATER
That concern over water conditions was not insignificant: In fact, the clients were adamant that no pre-packaged chemicals were to be used in treating the water – which, of course, had to be absolutely perfect in every possible way when the pool was in use, which would be no more than about a half dozen times a year.
To accommodate this mandate, Ruddy had designed the system with a combined saltwater chlorination/ozone treatment system.
Redundant Safety The pool described in the accompanying text was designed and built before the emergence of the Virginia Graeme Baker Pool & Spa Safety Act. Even so, our extensive experience in commercial pool construction had already led us to develop systems that effectively eliminate suction entrapment as an issue. We were pleased to have the basic support of system designer Kevin Ruddy (Omega Pool Structures, Toms River, N.J.), whose plans called for four-inch return plumbing. This enabled us to meet the desired four-hour turnover rate with a downsized pump – and to keep the line velocity well below the six foot per second threshold at which entrapment becomes an issue. Ruddy also called for a split main drain, thereby further minimizing entrapment risks. The clients had heard of and were quite concerned about the suction entrapment issue, so even the measures we took were not quite sufficient. Thus, in addition to taking advantage of the suction vacuum release system (SVRS) that’s built into the IntelliFlo pumps we used (Pentair Pool Products, Sanford, N.C.) for the circulation system, we also installed a separate SVRS device – just in case. As icing on the cake, the system is plumbed so that the main drains can be shut off completely when the pool is in use. This completes a broad-spectrum approach that makes us confident this pool will never be the site of a suction-entrapment incident. — W.D. & J.B. |
Given the use of the automatic cover and the extremely light bather load, there’s almost no demand placed on the sanitizing/oxidizing systems. Indeed, even with one of the systems turned off and the other running only a few hours a day, the ORP is always sky high, resulting in water that is extremely corrosive.
(Returning to the light rings for a moment: Most stainless steel products would be eaten up by the aggressive water, where the high-grade aluminum we used is one of the few available materials that can withstand such conditions.)
Basically, what this left us with was the challenge of dialing things back to a point where we weren’t perpetually over-treating the water and making it more aggressive than we wanted it to be. With some trial and error, we now have a routine where we leave the saltwater chlorination system off completely and run the ozone alone at an extremely low output level. (Given this special situation, we’re not concerned about maintaining the residual sanitizer level typically required with ozone systems.)
Those unique circumstances also led us away from installing pH-control or ORP systems. Instead, we monitor water conditions with hand-held devices when we come to the property for maintenance visits and make whatever slight adjustments the system might need.
Most of the circulation equipment was supplied by Pentair, including the cartridge filters and the variable-frequency drive pumps. Heating of the water to the client-specified temperature is handled by a heat-exchange system that runs off of a boiler used to drive a snowmelt system for the property’s terraces and driveway.
The clients have made it abundantly clear to us that they wanted absolutely perfect water quality any time they decided to roll back the cover and jump in. To make that happen, we stop by weekly to make sure everything is running to specifications, even though this pool is about as self-sustaining as can be.
So far, they’ve been more than happy with the results.
Despite their obvious pleasure, however, there are some pending issues we’re certain will involve some changes as we move forward. For one thing, the pool’s interior surface was a major source of back and forth among the clients and various design-team members. They wanted white – but they had a shade in mind as well as a material issues that was never fully resolved.
Mostly, they were concerned with reflections and how they’d work with the paint selected for the ceiling as well as the teak architectural woodwork. Discussions became so complex that we struck an agreement with the clients and the general contractor that we would plaster only with the understanding that whatever we applied would likely be replaced at some future date at an agreed-upon price.
So we installed ColorQuartz Classic White finish from 3M (St. Paul, Minn.). It has a great look and is somewhat less susceptible to damage related to water chemistry than is standard plaster. So far, the clients have stuck with it – but on this project, we’ve learned time and again that nothing related to aesthetics is ever truly settled.
THE SAME PAGE
The swimming pool we’ve covered here may be a simple rectangle and doesn’t even include a spa, so there will be some who will see it and leap to the conclusion that the project was a walk in the park.
Nothing could be further from the truth. Not only did we face down some interesting technical issues, but we also were working with clients who were actively involved in every decision – and often changed their minds midstream not only about what was being done but also about who was doing it.
The pool may be a simple rectangle, but the project was uniquely challenging on a number of levels. There’s a great deal of pride that comes from facing and overcoming such hurdles, and there’s also great joy that comes from being part of a grand collaboration, interacting with other professionals on the job site and producing such beautiful results. |
Along the way, some major team players came and went, but for whatever reason we always maintained and enjoyed a good rapport with them. It didn’t hurt that they maintained steady respect for Kevin Ruddy’s design work or that he was always there to back us up and help us navigate our way through the more difficult passages.
Had we been stuck with a pool designer who didn’t understand hydraulics, construction, water treatment or any of the other myriad issues that came up for question along the way, our lives on this project may have become intolerably difficult. As it was, we trusted Ruddy’s design, he trusted our execution of the program and the clients let us work things out without compromising our standards.
For us, this strongly reinforces the notion that quality results require quality people working together toward a common goal. In this case, what could have been a nightmare project evolved to become a sterling point of pride.
William Drakeley is owner of Drakeley Industries, a design and structural-shotcrete consulting firm for swimming pools, water tanks, tunneling, mining and other infrastructural shotcrete applications; and of Drakeley Pools, a specialty watershape design, construction and service firm – both located in Woodbury, Conn. Drakeley holds the distinction of being the first and, so far, the only American Concrete Institute (ACI) Certified Examiner for Shotcrete Placement from the pool industry. He is also an approved trainer for ACI-Certified Nozzlemen on behalf of the American Shotcrete Association (ASA), an ASA Technical Adviser, a Genesis 3 Platinum member and a member of the Society of Watershape Designers and its advisory board. He has taught numerous courses on shotcrete application at the Genesis 3 construction schools and is a contributor to Shotcrete magazine. Jeffrey Boucher is vice president and managing partner of Drakeley Pool Co. and Drakeley Industries. A 17-year industry veteran with expertise in all forms of pool design, construction and service, Boucher is an expert in green technology and alternative sanitizers and has contributed to industry articles on these topics. He also has a background in design and photography, and his work with Drakeley Pool Co. has been featured in national magazines including Cottages and Gardens, Fairfield Country Home and Luxury Pools. He is a participant in the Genesis 3 schools and is pursuing membership in its Society of Watershape Designers; he is also a member of the Nikon School of Photography and the American Shotcrete Association.