Material Standards
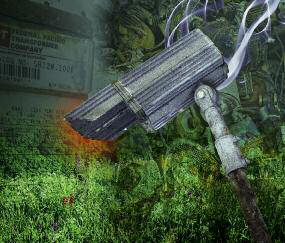
Call it human nature, free-market economics, the profit motive or whatever – the fact of the matter is that too many landscape lighting installers rely on low-cost products made with low-grade materials.
Obviously, they do it to cut down costs either to squeeze more profit out of each job or to bring the price down to the level required to get clients to sign on the dotted line. So rather than reduce the number of fixtures used on a project or even turn down a project altogether, they’re clearly willing to win a job by using equipment that has no chance of lasting more than a couple of years in the field.
I have no doubt that this is happening: In more than 20 years of working as a landscape lighting designer and installer, I’ve run across these cheap products countless times. And the upshot is always the same: I’m called to visit a relatively new installations that doesn’t work – and in too many cases can’t even be salvaged because, for example, transformers intended for indoor use have been used outdoors or because design compromises have been so severe that a site’s basic aesthetics are beyond help.
This willingness of some professionals to debase what good landscape lighting is all about is, I think, self-defeating. It may keep a company in business for a time, but it sets such a low bar for performance and reliability that the reputation of the entire industry suffers and even the ineffective players will ultimately vanish. The real bottom line? This approach hurts everyone, from the manufacturer and the installer to the consumer whose expectations have not been met.
MEETS THE EYE
The problem with products made with low-grade materials is that, in most cases, they do work – at least at first.
In other words, you can take the cheapest, flimsiest junk off the shelf at a store that sells irrigation or lighting products, install it with valid creative and aesthetic ideas in mind and, when the sun goes down and you throw the switch for the first time in the client’s presence, he or she will likely be overwhelmed – exactly as would be the case had the project been completed with professional-grade equipment.
That initial impression, however, is horribly (and even fraudulently?) deceptive. The “lighting expert” who perpetrates such projects seldom offers ongoing service as part of the installation contract, so there’s nobody to confront when, as inevitably happens, the system becomes problematic or stops working within a few months – or even within weeks in some egregious cases.
The client, of course, has no idea which products are inferior and all too often is left on his or her own to find another firm to set things right. I am occasionally called by these abused homeowners, and it’s a horrible situation in which any good feeling the client might have is gone. Moreover, the original specifier or contractor has squandered the opportunity to have a well executed project stand as a constant form of promotion of the value of landscape lighting to other consumers.
That’s just not right.
The quality of installed components truly makes a difference with landscape lighting, simply because the fixtures are exposed to more than just the weather. The plastic ground stake for the fixture at left, for example, wasn’t up to resisting repeated blows delivered by weed whackers and lawn mowers, while the high-quality brass fixture at right is made to take most of such challenges in stride. |
This is one of the reasons why, with every prospect I meet, I always stress the importance of working with professionals who at least offer maintenance packages: It is, I tell them, a demonstration of the contractor’s belief in the end product and signifies a willingness to ensure long-term client satisfaction.
Indeed, for those of us who have made that ongoing commitment, the very idea of using inferior products is unthinkable, basically because we know that it will end up costing us more, a lot more, in the not-so-long run to use inferior products up front.
Part of the problem is the aforementioned consumer expectations and the fact that lighting systems are available in retail stores at price points aimed at every level and budget. Some of the better stores may have a good array of products to sell across the full spectrum, but the average homeowner’s thinking is likely to be shaped by the lowest-cost items rather than the highest-priced ones.
If they get stuck conceptually at the level of the cheapest do-it-yourself-style products, it’s up to us as professional lighting designers and installers to inform them of the distinctions and focus their attention on what’s best for them for all the years they’ll own their homes. As I tell them, what they’ve been exposed to on the retail level are toys compared to truly professional lighting products: Yes, what I’ll be recommending costs more, but the equipment represents a far better value with respect to reliability and long-term performance and maintainability.
ON THE SHELF
Any lighting designer or installer worthy of being called a professional knows these product levels and their differences, and any who are willing to work with the toys really shouldn’t be in business. That’s an open-and-shut case.
As I see it, the real problem comes with in the middle or lower range with so-called “professional products”: These are often made by reputable manufacturers with good brand-name recognition, but to reach a more cost-conscious market they use lower-grade materials for their fixture housings and mounting hardware. These products basically cost about half of what top-of-the-line models cost – and, regrettably, they are marketed and sold as durable, professional-grade equipment.
Not all transformers and housings are created equal. The one at left, for example, was simply not capable of standing up to outdoor installation, while the one at right is set up to last through years of exposure to the most persistent insults nature and the elements can throw at it. |
While it is true that these items will last longer and perform better than the toys mentioned above, the fact is that these aluminum and composite materials simply are not durable enough for extended use in a landscape. For starters, most are still paired with halogen lamps, which generate tremendous amounts of heat and will, in time, break down the composite until they warp, crack, are no longer watertight, fail and decline beyond repair.
The other issue with composites is that they are all susceptible to the threat posed by gardeners. I respect these maintenance professionals and have a great many friends in that trade, but there is no escaping the fact that they tend to be very hard on lighting systems. They’ll kick fixtures, smack them with power tools, lash them with weed whackers, bury them in debris, bring down heavy limbs on top of them – or worse. On purpose or not, they’ll also dig up cables, break junction boxes and inadvertently do all they can to destroy lighting systems.
That’s bad enough when you have heavy-duty fixtures in place that can take the abuse, but when you use equipment made with light-duty materials and put them in harm’s way, it’s just a matter of time until significant damage and failures will occur.
This is why, if I see these products when I’m called in to evaluate existing projects, I won’t touch a renovation job unless the clients are willing to have me replace all of the low-grade fixtures with higher-quality versions. There is, I tell them, simply no way to fix the underlying problems while continuing to use products that at best represented a compromise when first installed.
METAL WORKS
The alternatives I define for these clients come in two forms: The first level includes fixtures made of non-ferrous (that is, non-rusting) metal that has been spun or stamped and turned to create housings. These are assembled using welds or stainless steel hardware, and the joints are sealed from the elements with various o-rings and heat-resistant sealant materials.
These products are superior to their composite and aluminum based cousins: They’ll stand up to some abuse and, when damaged, can generally be repaired. To be sure, they aren’t what I’d call top-of-the-line products, but I’d suggest their use in certain situations, as when a project requires use of dozens or even hundreds of fixtures and economizing makes sense.
I always make it clear to clients that these non-rusting metal fixtures still do require regular maintenance, as is true of all systems. I let them know as well that, although these products are reliable and durable, they don’t approach either the reliability or durability of the top products.
The problem at this level, I tell them, is that the metal stock can only be so thick when it goes into the bending and stamping processes. Moreover, seams secured by welds or screws can become weak spots when exposed to the elements and/or to repeated abuse by gardeners and their crews.
This leads us to discuss the top level – products I use wherever and whenever I can.
These fixtures are made of fully cast bronze, copper, brass or stainless steel. Casted metal are the key words here: These fixtures are made in foundries, typically die-cast or fabricated in sand molds, and are so thick-walled and heavy-duty that they’ll stand up to almost any type of physical abuse. Not even a motivated gardener will win this contest!
Beyond Fixtures The cables used in landscape lighting systems are among the most consistent products I’ve ever encountered: If the product is rated by the Underwriters Laboratories (and, frankly, even if it’s not – although I’d never advocate the use of non-UL-approved cable) ), the copper used in cable is always going to do its job. In all my years in this business, in fact, I’ve never once experienced a short in any cable that comes off the spool. Yes, there are differences in sheathings and coatings and some are easier to use than others, but in my experience, cable made for direct burial in general and for landscape lighting in particular can be used with great confidence. For all that, once it’s been in the ground for a while in direct contact with soil, it loses some of its flexibility and the sheathing may become hard and brittle – a point to note well if you’re called in to do extensive work on an existing system. (A side note: As I’ve mentioned before in these pages, I’ve taken to installing all my wiring in conduit. Not only does this protect the cable from damage, but it also makes installation and replacement easy. Direct burial is the accepted industry standard, but I prefer this approach.) Transformers, by contrast, are different animals that are made to less rigorous standards when not specifically manufactured and listed for landscape lighting use. This is a place where contractors can save a lot of money, but, personally, I recommend and install only high-end products that are designed specifically for landscape lighting use and have interior terminal lugs that accommodate multiple cable runs. Without getting too specific here (given that transformers are a fairly complex topic unto themselves), let me draw some clear lines in the sand: First, pay attention to the enclosure. Some boxes intended for outdoor use consist of painted steel that just won’t hold up to the elements. Instead, I use stainless steel, fully gasketed boxes that will perform reliably for years without creating any safety hazards. Second, use only transformers designed and intended for outdoor use with proper, built-in primary and secondary circuit breakers or fuses. To do otherwise is to expose your clients or their landscape-maintenance crews to significant risk of severe injury (and yourself to possible liability). The frightening difficulty here is that most states (including California, where I work) have no permit or inspection process for low-voltage landscape lighting. Bottom line: Transformers used in outdoor applications must always have been designed and intended for outdoor applications – no exceptions! — M.G. |
As true professionals, these are the products we must strive to use. Yes, they are expensive – twice or three times as costly as inferior products – but I describe the difference to my clients as an investment in service life, serviceability and long-term satisfaction. Nowadays, I say, I’m currently servicing fixtures of this kind that I installed twenty years ago. Yes, I’ve replaced lenses, lamps, seals, o-rings and the occasional socket, but the fixture housings and mounting hardware are still rock solid.
And in situations where time and abuse have taken a toll on aesthetics, it’s seldom a big deal to remove these fixtures from the site and send them to a metal shop for sandblasting and application of a fresh chemical-stain finish. Once such fixtures are refitted with new wiring, o-rings, lamps, lenses and sockets, they’re basically good as new (if not better).
In other words, with proper maintenance, these are the products that last indefinitely. They may become weathered and oxidized, but if you open up even an old one of these fixtures, you’re likely to see an inside surface that looks somewhat new.
NO IGNORANT BLISS
The difference between fixtures made with cast non-rusting metal and all of the available alternatives are so great that I find it difficult to accept the thought of using lesser-quality materials at the professional level.
I am so dogged on this point that it upsets some of my colleagues, but I look at it this way: Landscape lighting systems are not unlike most watershapes in that neither are necessities of life. These are luxury products, and therefore they are not something every home should have simply because not every homeowner can afford to have the job done right.
In this limited marketplace, I consider every system I install (and then subsequently maintain) to be a marketing device for my business. As a result, I want them to work properly so that, when potential clients see them, they will want something that performs just as well.
This entire referral dynamic breaks down completely when a system doesn’t work.
Although some will say I’m being too rigid, I think it is better to walk away from a job when the clients don’t have the budget to do things right (or are unwilling to pare back on the system and their expectations) than it is to move forward and do substandard work that will not perform in the long run.
Yes, times are tough, but if we professionals really do want to lay foundations for better times, the only reliable way is to deliver quality in all aspects of what we do. In this business, that means starting with the raw materials from which our products are made!
Even if the products you use in your designs don’t have your name on them (as mine do), you should treat them as such because your projects can be no better than the weakest link in the systems you develop. And if that weakest link is related to system is reliability and longevity, it’s easy to see that these product choices have a great deal to say about the ultimate success of your business!
Mike Gambino owns and operates Gambino Landscape Lighting of Simi Valley, Calif. A licensed lighting contractor since 1990, he has specialized since 1995 on high-performance low-voltage systems. He may be reached via his Web site: www.gambinolighting.com.