The New Green Building Code
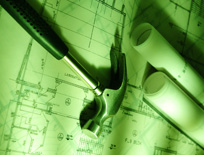
The state of Rhode Island and the city of Richland, Wash., recently adopted the International Green Construction Code (IGCC) as part of their building codes for commercial buildings.
That might not sound important if you don’t happen to work in either of those small markets, but it’s the tip of a big green iceberg toward which your company’s ship is sailing at full speed. As the IGCC becomes more recognized, many other states, counties and cities are sure to adopt it as part of their building codes.
The International Code Council (ICC) is the organization that developed the up-and-coming IGCC as well as the International Residential Code (IRC) and the International Building Code (IBC), which are pretty much the law of the land in the United States today.
The ICC was founded about 15 years ago, and it developed the IBC to replace three then-existing model codes. In 2009, it began to develop the IGCC when it became apparent that the demand for “green” buildings wasn’t going away anytime soon.
Although it is still technically a draft and won’t officially be published until early 2012, the IGCC is available for adoption into local building codes now. The current edition (Public Version 2.0) was finalized in November 2010 following lengthy hearings on all the changes proposed to Version 1.0. (If you have any arguments with the current IGCC, now’s the time to submit comments.)
Now, much as I hate to do so, let’s make this a little more complicated: The Portland Cement Association, feeling that the IGCC did not go far enough in emphasizing the need for durable and disaster-resistant buildings, developed its own sustainability code requirements — called High Performance Building Requirements for Sustainability (HPBRS) — and formatted it to be adopted as modifications to the IBC.
The high-performance buildings they have targeted are government buildings, especially schools. Obviously, PCA’s goal is to promote the use of concrete, so they argue that durability is sustainability, because the lowest-impact building of all is the one that doesn’t get built. Concrete buildings last longer, so they are more sustainable.
As much as I like the HPBRS, contractors who work with concrete are more likely to be faced with the provisions of the IGCC — a very complex document. It starts with a large list of minimum requirements, and then each jurisdiction has the option of selecting additional requirements to meet local goals. Finally, there’s another set of project-specific “electives” that add even more requirements. I’m not going to get into the jurisdictional requirements or project electives here, but be aware that these provisions could apply to your projects.
Below, I have very briefly listed the IGCC requirements most likely to apply to you. Look them over, download a copy of the IGCC and get familiar with it: Remember, if you don’t like something you see, now’s the time to submit your comments to the ICC — or send them to me and I will submit them.
The IGCC website is at www.ICCsafe.org; PCA’s HPBRS is available at www.cement.org.
How the IGCC Affects You
Most of the requirements in the IGCC that could apply to concrete contractors are not really that new. In fact, they are often things you already do.
402.3.2 Stormwater management — This requires all rainfall to be managed on-site, which will give a big boost to pervious concrete hardscapes.
402.3.6 Building site waste management plan — This requires recycling or salvaging of not less than 75 percent of land-clearing debris and excavated soils.
403.1 Walkways and bicycle paths — These must connect to existing paths or sidewalks, and they must support storm-water management infrastructure, including pervious pavement.
404.2.1 Site hardscape materials — Hardscape must have a Solar Reflectance Index of 29, which light-colored concrete does. Pervious concrete pavements are automatically deemed to comply.
406.6 (2.4) Landscape, soil and water quality protection plan — This requires contractors to prevent runoff from leaving the construction site, including concrete wash water.
502.1 Construction material and waste management plan — At least 50 percent of construction waste must be diverted from landfills.
503.2 Material selection — At least 55 percent of the total building materials used in the project, based on mass or cost, must be recycled or locally produced.
505.1 Building service life plan — This requirement provides concrete with an advantage because of its long service life. IGCC requires a minimum service life of 60 years with an option to upgrade to 100 or even 200 years.
601.3 Minimum requirements — Buildings need to comply with the International Energy Conservation Code. Concrete is a good choice for its air-tightness in walls and thermal mass as flooring.
608.7.1 Buried piping — Domestic hot water pipes in or below a slab must be insulated.
804.2 Radon mitigation — The IGCC has a long section on radon mitigation and a table of the counties where the section applies. If you work in one of those counties, you’ll need to install a radon mitigation system under any slabs, consisting of a minimum 6-mil polyethylene membrane (I recommend 10-mil minimum) on top of the sub-base materials; polyurethane caulk around any slab penetrations (such as pipes); sealing of all joints (control, isolation, construction); and vent pipes within the sub-base that terminate above the roof.
805.1 Scope (in Asbestos Use Prevention section) — Any materials containing asbestos are prohibited.
806.2 Adhesives and sealants — The VOC maximum for architectural sealants is 250 grams per liter.
806.3 Architectural paints and coatings — The VOC maximum for concrete curing compounds is 350 grams per liter and for concrete and masonry sealers is 100 grams per liter.
806.4 Flooring — Here’s where concrete floors have an advantage, since 85 percent of an interior floor area must meet VOC requirements, but concrete flooring is simply “deemed to comply.” The same goes for concrete wall systems in section 806.5.
807.1 Sound transmission — This section offers another advantage for concrete, since concrete walls are naturally more sound-resistant than wood-frame walls.
— W.D.P.
William D. Palmer Jr., P.E., is with Complete Construction Consultants, where he develops technical and educational resources for the construction industry. He can be reached at wpalmer@cee3.com.
This is another in an ongoing series of articles adapted with permission from Concrete Decor magazine. For more information on the magazine, visit www.concretedecor.net. For details on the Concrete Decor Show & Spring Training and its extensive educational program, go to www.concretedecorshow.com.