Safely Elegant
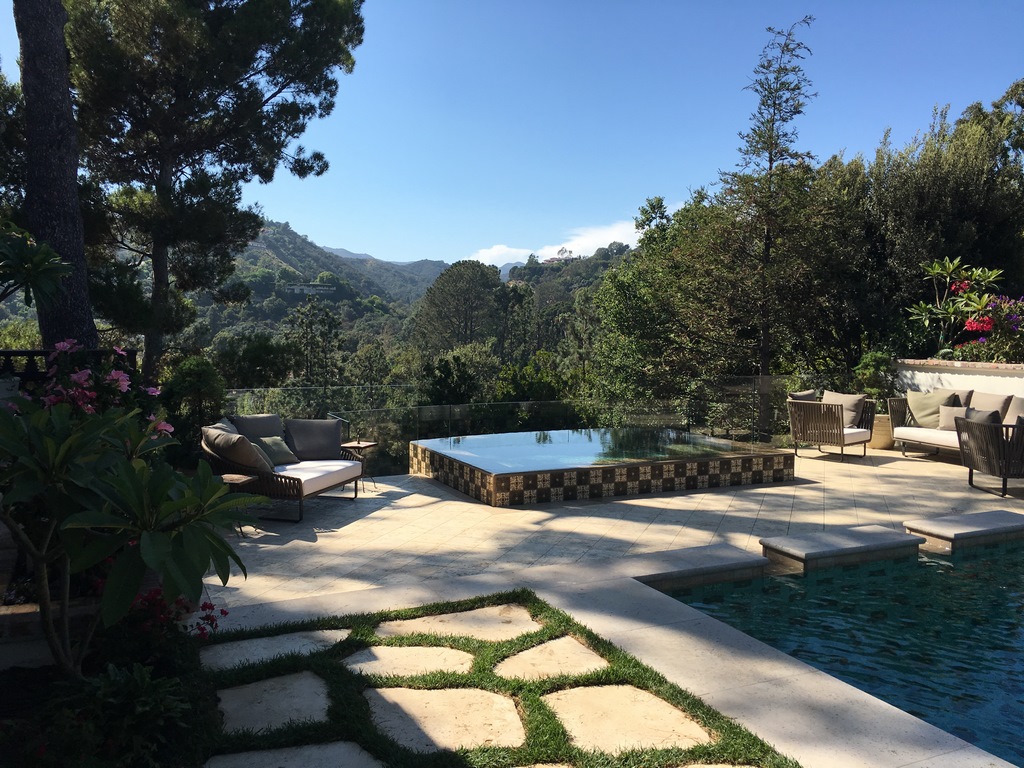
An Interview with Alison Terry, Dave Penton & Jimmy Reed by Jim McCloskey
The first time I visited this backyard, the pool was complete and beautiful, but there was one discordant detail: Along the far end was a wooden fence that cut off the view. I was there with tile specialist Jimmy Reed, and this wasn’t a feature he mentioned. So, being both polite and sufficiently dazzled by the pool, I didn’t bring up the sore thumb.
The next time I saw the backyard, I immediately figured out that the fence had been a temporary detail: I was there with pool builder Dave Penton, who at the time was well into construction of a structure beyond and below the intrusive fence. The sturdy, permanent-seeming barrier was there to keep the kids out of harm’s way and now made perfect sense.
The thing that had confused me was the fact that the fence was lovely and seemed permanent because it had obviously involved some detailed construction. If it had been orange-plastic site fencing, its purpose would’ve been obvious. But what I understood quickly is that aesthetics mattered on this project, down to the last detail. And if the barrier was to be there for months, it had better look good.
What was happening on the far side of that fence was pretty special, too, and that’s where we pick up the narrative we left off at the end of the first article (click here) in this two-part series – beginning with some background from landscape architect Alison Terry.
– Jim McCloskey
Alison Terry
The spa part of the project started with some controversy: When we first presented our plan for inspection, the city told us we couldn’t build a spa out on the slope because it infringed on the setback. We thought this was really odd, particularly given the fact that the homeowners had already received a permit to build a guest house in pretty much the same exact space. What difference did it make if the structure served as housing or held water?
This is an instance where Corey Ruppert, the project manager, truly earned his keep. Working with architect and structural engineer Mark Smith, he went back and forth with the Building Department and finally won a variance because we would simply be placing the spa as an “accessory” atop a new structure – which was now to be the equipment room rather than a mother-in-law-type apartment. It was a thin distinction, but turning the inground spa into a rooftop spa made all the difference.
Just past the ornamental fence, the slope had already been carved out – originally for a small apartment, but now for an equipment room with a rooftop spa. With the underpinnings set, the shell came together for the eventual installation of a moveable spa floor. It’s essentially a deep, perpendicular-walled tank with extra layers of plumbing, but it all had to be prepared to within the tiny fractions of an inch to which we’d committed ourselves to speed the manufacturing process. |
None of the patio space beyond the pool and around the spa existed before the project began. Working with the vertical gap gave us the ideal hiding place for all of the equipment as well as the surge capacity for the pool spillways and the perimeter-overflow spa.
Dave Penton
The first phase of our spa discussions and the related work on site had to do with safety for the clients’ young daughter. They wanted the spa out on the edge so they could sit in it while enjoying the panoramic views, but the property sloped down sharply. The homeowners didn’t want a big fence to come back in and disrupt the view again, so we all put our heads together and rolled through what seemed like a dozen good safety possibilities before raising the Hydrofloors option.
At the time, Paolo Benedetti – a fellow designer/builder from northern California – was working with Hydrofloors, a company based in the United Kingdom that makes mechanisms that elevate floors within a given space to make water levels adjustable. The cool thing is that the mechanisms can operate on separate levels, so the floor and benches of a spa could be set at whatever positions we desired and could still rise to form a solid, seamless, totally flat surface either under a thin sheet of water or completely dry.
We brought it up with the clients and they were interested enough that we brought Paolo in to make a presentation. The clients loved what they heard and went for it – and this was despite the fact that it was, by a long shot, the costliest of the options we’d considered.
A.T.
We learned two important things about these clients as time went by. First, they loved things that were cool. Second, they wanted them yesterday once they made a decision.
D.P.
That need for speed put us in a spot, because Hydrofloors’ usual procedure is that they come in once the containing vessel is complete in every detail, take meticulous laser readings of the dimensions and contours, send the information to their manufacturing facility for four months of fabrication and assembly – then put everything on a boat to a facility in Belgium for finishing touches before shipping the product to the United States. The process can take many months.
With the shell’s surface painstakingly prepared, it was time to apply an interior finish made up of the dark shade of the Moroccan-style tile we’d used in the pool set atop a large-format black tile that would be hidden by the floor mechanism. While these tasks moved along, the catwalk was being completed around the leading edge of the spa, as were the three spillways that flowed out of the pool to provide subtle sounds on the deck when the spa isn’t in use. |
We couldn’t wait that long, so we had them send us specs that we agreed to meet to tolerances within tiny fractions of an inch. It was a risky approach, but we knew we could trim several months off the usual process – months that would make the clients both happy and patient because they knew what they were getting would be special beyond belief.
A.T.
One of the biggest challenges I faced as a designer was how to make the spa safe when the floor was up all the way, given that someone could walk on top of it and might fall over the edge and down the slope. The solution was pretty simple: We put a catwalk down below the spa and set a 42-inch tall glass fence at the outside edge of the catwalk.
This new, lower level was 29 inches below and three feet beyond the spa’s outside edge, so it was positioned so it can’t be seen by anyone sitting in the spa. The catwalk was a tricky addition for all sorts of structural reasons, so Mark Smith and Corey Ruppert were heavily involved, as was Dave Penton.
This was only one of many times we all had to put our heads together and invent a solution. The result in this case is a system that met all goals, particularly the clients’ desire for safety and their equal desire to maximize the beauty of canyon views from the spa.
Jimmy Reed
The key to this spa adventure is that we had to be dead on with every detail of the structure’s interior finish – not to mention making certain the structure was entirely waterproof for a rooftop application.
The container itself was pretty simple: It’s essentially a tank with a flat floor and perpendicular walls. The only complexity came with the arcing profile of the far wall, but that was mostly a matter of preparing the large-format porcelain base tile we were using to follow the curvature. The tile that would be seen when the spa was functioning – a solid field of one of the tiles we used in the pool – was small enough that we had little trouble making it work.
The process of installing the Hydrofloors system began with construction of a crane mechanism to transfer heavy components from the deck into the spa. Once the floor was in place, we immediately began inserting tile atop and between the floor modules to make certain all was well; we also completed the spa’s exterior facing and began the process of adding tile to the top of the shell. |
The difficulty – and this was something that pulled the entire design team into the act – was looking at the spa from above and figuring out how to set up the well and benches so that, when the spa was “closed,” the flattened tile pattern worked precisely, with no visual disruptions. It was a bit of a puzzle because of the multiple floor pieces involved, but it came together beautifully.
There was one issue: The Hydrofloors system has trays that hold the tiles using a special adhesive the manufacturer provided, but the trays weren’t made to accommodate the hand-made tile we were using. It was thicker-than-standard material to begin with and also had some irregularities in thickness, so we had to spend time grinding material away from the backs of the tiles to make them fit – and become level to within a sixteenth of an inch so the spa could serve as a decorative, reflective surface with water brimming over the perimeter or serve as a safe, dry platform for play or relaxation.
A.T.
The three rills flowing off the end of the pool became an issue, too. As was mentioned before, the original intent had been for tiny trickles of water to flow over the weirs as a subtle vanishing-edge effect to pull eyes out toward the distant views. But the clients decided they wanted more sound when the spa wasn’t in operation, so we boosted the flow. The result is that we needed to include a surge tank to handle the increased volume – another system-design adaptation that kept us focused late in the game.
D.P.
The clients were funny about steady progress. After months of disappointment with the molasses-slow pace of the original pool contractor, my guess is that they learned their lesson and just kept after us to keep showing meaningful progress. With the pool, for instance, we decided to apply a cure-enhancing compound because it meant Jimmy could get to work inside the shell without several weeks’ delay for the usual shell curing.
With the spa’s floor raised to full height, we completed tile installation along the arch of the front section and began the painstaking process of adding tile to the top of the floor’s multiple trays – a process significantly complicated by the need to make hand-made tile of inconsistent thickness level to within a tolerance of a sixteenth of an inch. We saved some of the final cuts for completion with the floor in a lowered position and completed tiling of the vertical surfaces of the benches. Before long, the spa was ready for filling and final system checks. |
This is the main reason we made a commitment to Hydrofloors that we would exactly meet their specifications in our construction. It was a huge but manageable risk, and we shaved weeks and probably months off the timeline by going for it.
J.R.
The thing I know about tile work is that it takes its own sweet time. Between careful surface preparation and meticulous application, a project of this magnitude can stretch out long enough that it can try a client’s patience. The key here is, while the clients wanted a good pace, they also wanted superb results.
They kept a close eye on the way things were unfolding and knew from watching us that we were moving at what they could sense was an appropriate pace, even if somewhere deep inside they might have wished we were going faster. As they saw how things fit together and how the overall space was steadily taking shape, I don’t think they exactly relaxed, but I do think they became a bit more patient.
A.T.
We went through that same sort of acceptance process with the landscape. The clients love full, lush greenery, so we removed some of the original hardscape and added new plantings. We also retrofitted several existing walls to create more planting areas. All of this involved waiting as things grew in.
We followed the original plan with one exception: They didn’t want hardscape to surround the pool on all sides, which led us to insert a lawn area between the pool and the cabana. In that green swath, I had proposed a somewhat formal system of stepping pads, but they pushed back and let me know they wanted something more random, rustic and natural. As they pointed out, there was a similarly random pattern in a side yard – so it made sense to them and wasn’t a place for me to draw a line.
Although much of the accompanying text has been about tile application and the features of a moving floor, throughout the process the project team had its sights set on great beauty and serenity through our selections of hardscape materials and plants while managing lines, shapes, motion, sounds and colors along the way. It was, from the beginning, all about performance on every level – and our desire to please clients who encouraged us to find the best possible solutions, over and over again. |
There was a definite look to the property and its architecture. We worked with it, which was one of the reasons we recommended ripping out the old pool and starting fresh instead of going through an awkward refinishing project. Our intention was always to make our additions or new work blend in to make it seem as though everything was built or planted at the same time as the house.
D.P.
We carried that thought pretty far, in fact. For example, we inserted what look like big, old-school lighting niches in the pool, just to give it a classic feature right down the Grecian style of the bright-chrome rings around the lenses. But they aren’t lights: They’re actually underwater speakers that we installed to go along with a separate, state-of-the-art lighting and control system.
Fellow Travelers There’s no way we could’ve made this project work without the unflagging support of Corey Ruppert of Salt Mine Design Build (Topanga, Calif.). His work as project manager and his skill with CAD design made the spa in particular a reality. Mark Smith of Mark L. Smith Architects & Engineers (Tarzana, Calif.) was there for us in resolving structural issues related to the whole project – but he was always on top of things with the spa. Paolo Benedetti of Aquatic Technology (Morgan Hill, Calif.) was another force behind the Hydrofloors portion of the project, making connections for us and easing the minds of his European counterparts that we could hit the specifications they gave us. Finally, a mostly anonymous Utah tile artist came through for us in amazing ways. Our thanks to Country Floors’ Los Angeles office for making it all work. — A.T., D.P. & J.R. |
There are also some nods to visual consistency as well, including Jimmy’s approach to hiding the suction lines behind a tiled frame as well as a small, swinging panel that hides access to the plastic fitting needed for the automatic pool cleaner.
A.T.
We did occasionally break with our “classic” approach to the pool, but we went fully modern with the spa, particularly with the perimeter overflow, using the arcing wall of the far edge to soften the look and tie it back into arched forms seen on both the house and the cabana.
We rationalized this “update” with the knowledge that many Moorish-style waterfeatures throughout history have had perimeter-overflow fountains – our fresh interpretation of ancient forms and techniques.
J.R.
For me, the bottom line on this project – both parts – is that it was always fun. Watching the clients as it came together was about as satisfying as it gets, and their increasing enthusiasm kept driving us to get everything just right on every level.
This collaboration was great fun, and what I look for more and more is the opportunity to work with colleagues who know what they’re doing and make the whole process unfold smoothly with minimal drama. In retrospect, however, what I’m happiest about is that I answered my phone despite being on vacation and brought together a great team to work wonders for a great client. It doesn’t get any better.
Alison Terry runs Terry Design, a landscape architecture firm in Fullerton, Calif. She received a Master of Landscape Architecture degree from the University of Virginia and is a member of the American Society of Landscape Architects, representing its southern California chapter as liaison to the Historic American Landscape Survey. Terry is also a member of the board of the Mediterranean Garden Society. She may be reached through her web site: www.terrydesigninc.com. Dave Penton is the founder and president of Fluid Dynamics Pool and Spa in Fullerton, Calif. A specialist in residential watershape construction in and around Los Angeles and Orange counties, he is known for his attention to detail for innovation with mechanical systems. A graduate of Genesis University and a master in the Society of Watershape Designers, he is now a Genesis instructor. Jimmy Reed is president of Rock Solid Tile, a tile design/installation firm based in Calabasas, Calif. He founded the company in 1985 after spending his teens and early 20s learning the tile-installation trade. In between, he attended Art Center College of Design (Pasadena, Calif.) and spent several years working in the entertainment industry. For the past 30 years, Reed has focused most of his creative energy on designing and installing tile finishes for high-end custom watershapes, a process that has seen him work with some of the industry’s leading designers and builders. He may be reached through his web site: www.rocksolidtile.com.