Hillside Smarts
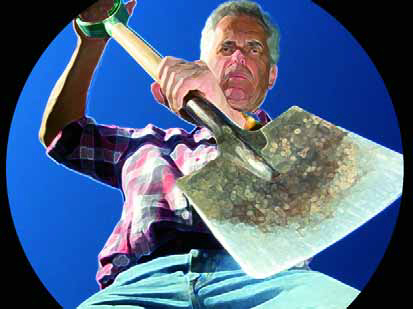
In last month’s introduction to what it takes to prepare for, organize and complete the excavation stage of the watershape-construction process, basic common sense was the governing factor in how the process should proceed. What I was discussing last time, however, was simple, flat-site excavations – cases in which access is commonly not an issue, soils are often consistent across a site and the potential surprises are relatively few.
This time, my focus is an altogether different breed of excavations – that is, the task of preparing a sloping, hillside site for installation of a watershape. This process offers
a set of challenges that is not for the faint of heart – something certainly to be avoided by beginners and even by many experienced builders.
Hillside projects are notorious for elevated risk of structural failure, for the extensive substructures of piles and grade beams they often require and for sites often characterized as “difficult” with respect to equipment access. To make a long story short, working in these conditions is inherently harder (and potentially more dangerous) than is excavating on flat land.
At the same time, these projects tend to go smoothly – and for at least two good reasons. First, their complexity makes me perform at the absolute top of my game as I deal with hundreds of details rather than the dozens that might be encountered in a flat-site job. Second, the expert support I gain from soils and structural engineers as well as from inspectors, building departments and the top-flight subcontractors who get involved in these projects puts 50 pairs of eyes on the tasks at hand in addition to my own.
STEEP INCLINES
The project seen in the first set of images accompanying this column is a classic example of what can be described as a “tough” excavation.
Set in the Hollywood Hills, the design called for a pool/spa/deck structure to be cantilevered off an extreme, fall-away slope into which we dug a set of piles that reach down to competent soil (as determined by the soils engineer). In all, this required us to remove about 30 cubic yards of material – not a huge volume compared to many standard excavations but in this case quite a lot.
The main complicating factor here was access, which was extremely limited for this site: There was absolutely no way we could bring in a drilling rig, so all of the piles had to be dug by hand in a process that put brave, strong, skilled laborers down into the holes with chipping hammers, shovels and buckets used to carry off the spoils. There’s no way to pretty this up: It is brutally hard, terribly confining and potentially dangerous work.
This site offered both a steep slope on a fragile hillside as well as extremely limited access, so digging for the piles and grade beams that would be needed to support the watershapes and decks was done by hand. These are delicate operations requiring a knowledgeable, experienced crew and equally knowledgeable, experienced supervision. |
In all, the pool’s foundation required us to dig six of these holes to contain what are known as friction piles, which are like huge paper-towel rolls filled with structural steel and concrete. We might alternatively have gone with bell caissons, which, as the name suggests, have a widened, bell-like area at the bottom to increase surface area, but the choice here was friction piles: These have uniform diameters top to bottom and are far easier to dig despite the fact they require somewhat greater depth.
Hand-digging of this sort is an area in which OSHA requirements must be followed to the smallest detail. While some see dealing with this agency as a chain of endless hassles, in the case of hand-digging piles, OSHA’s guidelines can literally spell the difference between life and death for the intrepid souls who are willing and able to work in three-foot-diameter holes at up to 30 feet below grade.
One of the key safety issues, obviously, has to do with shoring up these pits to prevent cave-ins. We generally use corrugated-aluminum tubes that slide down into the holes as they get deeper, but you can also use thick-cardboard SonoTubes or even wooden shoring. As a rule, cave-ins happen at the upper levels of a hole where the vertical pressure of the soil isn’t sufficient to lock the earth in place. OSHA, however, requires support all the way to the bottom, doubtless because experience has shown the regulators that the risk is too great otherwise.
NO ROOM FOR ERROR
Hand-digging these holes is definitely not a one-man operation. Typically, the man in the hole is supported by another at the top who is constantly raising or lowering a five-gallon bucket with a rope to remove the spoils and, of course, to insert or extract the person down in the hole. This ground-level person also serves an important safety function, communicating steadily with the worker below to make certain all is well and pulling the worker back to the surface if signs of fatigue or oxygen depletion become apparent.
That last point is important: Depending on the depth of the holes in question, we’ll set up an oxygen line and will even drop exhaust fans into the hole because the air can get depleted pretty quickly in confined spaces at depths more than 20 feet below grade.
Hand-digging adds another factor to the mix: A worker in the bottom of a hole needs a diameter of at least 36 inches to complete the task effectively and efficiently. This requires early communication with structural engineers, who typically assume that a site offers adequate access and so will often specify 24-inch piles.
Fortunately, many sloping sites offer good access – as in this case, where we were able to bring a drilling rig onto a well-prepared, well-marked site and complete the excavation for a string of deep piles with relative ease. |
If a plan calls for these 24-inch piles and you bid the job that way but there’s no access for a drilling rig, then you have a huge problem because of the extra expense involved in labor, time, materials, forming and everything else involved in this construction phase. This is a case where knowing all about access issues ahead of time not only determines the logistics of the operation, but the actual design itself.
This is not, in other words, an area in which corners can be cut or you can learn as you go: Knowing what you’re doing when you need to dig 25 to 30 feet down into the earth on the side of a hill is absolutely crucial because, eventually, what you’re doing below grade will determine the reliability and longevity of the structure that will appear at and above grade.
Even with a plan, however, you sometimes run up against the old axiom, “Sometimes you get the bear; sometimes the bear gets you.” A skilled laborer with a chipping hammer can be amazingly efficient and delve into the earth with surprising speed, but there are limits: Some types of extremely hard material cannot be penetrated by hand, and sometimes a site calls for a hole that reaches too far down for a person to dig (our safe limit is right around 30 feet).
True, it rarely happens if you know what you’re doing and the soils and structural engineers have done their jobs well, but every once in a while you end up with a design that simply won’t work as planned – at which point the client has a big decision to make. Anything can be built if that client has the resources and the will to cover the increased cost of getting the job done, but there are times when the numbers become so large that the client will call things to a halt.
Whatever happens – stop or go – rest assured that, in the face of unexpected difficulty, fudging on either the design or the structure to get a project built is never a good notion.
THE LAY OF THE LAND
As suggested above, even the best planned of these hillside projects can run into the unexpected – such as a section of soil impenetrable by hand.
Hillsides also commonly encompass a variety of soil conditions within the same site. It’s not unusual, for example, to encounter all sorts of odd bedding planes, layers of alluvium, various cut-fill transitions and a range of other conditions that might have an effect on the structural design that will send you back to the drawing board.
This is why, whenever I’m building a hillside structure, I make it clear to the homeowners that this is not an area where they can think in terms of saving money. I let them know we’re going to design a reliable structure based on soils testing and proper engineering – no ifs, ands or buts – and that I’ll walk away from the project without the slightest hesitation if they can’t accept that fact.
There are lots of different drilling rigs and all sorts of attachments designed for penetrating certain types of material. In selecting a rig, going with the biggest, most powerful unit that can fit on the site is usually the best and most efficient approach, while choosing the right attachments is something to be determined by a soils engineer familiar with the site. |
I also let them know, as with the possibility of running into an impenetrable obstacle, that their project might run into something unexpected – something that stands a chance of substantially increasing costs to the point where they might have no choice other than back away and rethink everything based on the site’s limitations.
Fortunately, not all hillside projects are as unforgiving as the one shown in the first group of photographs on these pages. In most cases (as in the second group of images), you can find a way to move a drilling rig into position and make much shorter work of the excavation.
Any drilling rig will do at a pinch, but as is the case with most tasks requiring equipment, bigger and more powerful is always better than any alternative.
Drilling rigs come in a helpful range of sizes and are extremely efficient. You can drill holes in a matter of hours that would take muscle and sinew days to complete. That’s why, if there’s any conceivable way to get a drilling rig where it needs to go, I’ll always bring one in wherever possible: The expense is always worth it.
Once you have a rig in place, of course, you still need to know what you’re digging into: There are a variety of bits and augers suited to delving through different types of material – something for the engineer to determine. Again, this is an area where absolute knowledge of the site and its soils is essential.
TOO SENSITIVE
Allow me to make one enormous point about all this: Hillside excavations are so tricky and so individualized to the site and its characteristics that it would be irresponsible of me or anyone else to try to be prescriptive in a magazine article. This is not an aspect of watershaping you can learn that quickly or easily.
Where it’s unfortunate when a firm works beyond its ability in excavating for a standard, flat-lot project, with a hillside project, “unfortunate” becomes “criminal.” Not only will the homeowners end up with a project that will fail – sometimes spectacularly so when entire structures give way and fall down a hillside – but you as a watershaper can also literally kill people on these jobs if you don’t know what you’re doing.
Short of that, you can waste unimaginable sums of a homeowner’s money, ruin your reputation and end up spending years in litigation, because failures in these cases have an ability to cause incredible amounts of property damage not only for your clients, but also for neighboring properties. And when you factor in the risk of serious personal injury to workers, it becomes clear that this is not work for the timid, the unskilled or the uninformed.
I would argue that every watershaping project calls for proper engineering and on-site management at every step of the way, but that’s even more critical on hillsides, where everything from anchoring heavy equipment to removing the spoils from the site must be carefully orchestrated.
Simply put, hillside work is absolutely no place to practice or learn on the job. Every single person on your crew should be experienced, and if you yourself are not up to speed on the fine points of all project phases, you and your clients will be far better off if you step back and bring someone in who has the expertise and experience required to guide a project through this phase.
If you do so, pay attention to what happens: You might not be ready to tackle the next project solo, but you’ll pick up valuable lessons you can apply the next time you need to organize a hillside excavation.
David Tisherman is the principal in two design/construction firms: David Tisherman’s Visuals of Manhattan Beach, Calif., and Liquid Design of Cherry Hill, N.J. He can be reached at [email protected]. He is also an instructor for Artistic Resources & Training (ART); for information on ART’s classes, visit www.theartofwater.com.