Vinyl Lines
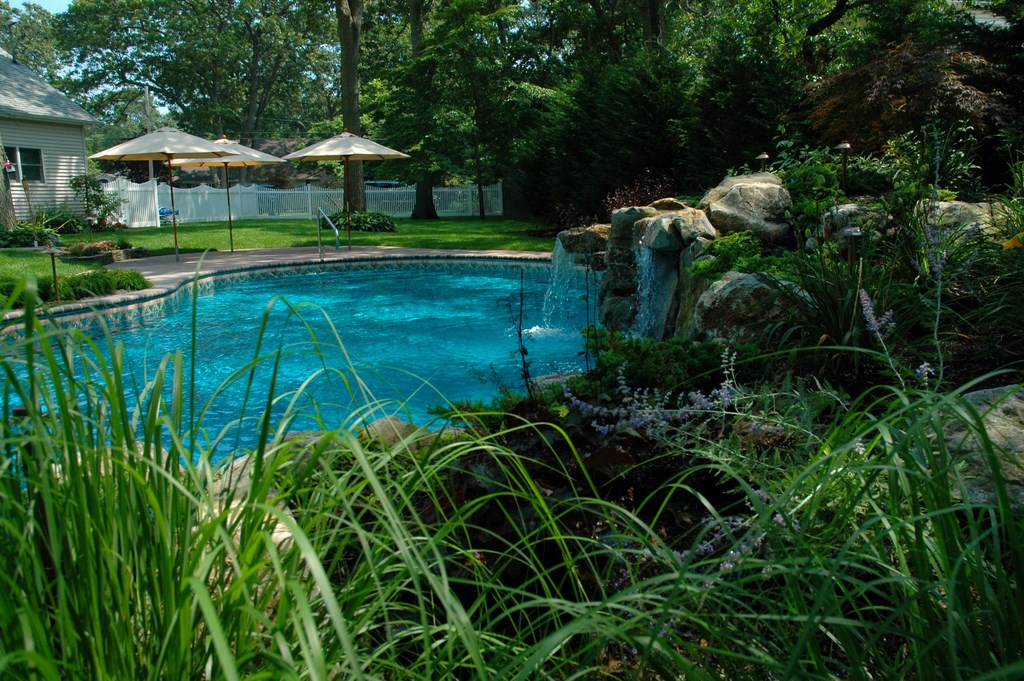
It’s no secret among those who’ve been in my segment of the watershaping industry as long as I have that vinyl-liner pools weren’t as attractive as their gunite counterparts in the old days: The finishes weren’t very interesting, options in colors and patterns were limited, the only type of coping we used was made of aluminum and most liners were only available in rectangular configurations in a limited number of standard sizes.
Despite those shortcomings, however, vinyl pools caught on, and in a big way, and I have watched every stage of that development for the more than three decades I’ve
been in the vinyl business. (My company True Blue Swimming Pools of Northport, N.Y., has been in business, 16 years.)
These pools became particularly popular in the northeastern United States, where freeze-thaw conditions and a host of specific market factors made these comparatively inexpensive vessels quite popular. But even with widespread use, for many years there were few advances in shapes or looks, and these pools simply did not provide customers with much by way of design options. Indeed, for most of my time in business, we’d cede true custom work to gunite or shotcrete builders.
In recent years, however, all this has changed. With the advent of computer-aided drafting technology and computer-driven manufacturing techniques as well as advances in the ways steps, benches and spas are made, vinyl-liner pools can now be made with virtually the same level of design flexibility as can concrete watershapes. They are still seen as an affordable alternative, but there’s no question that the vinyl industry has been bringing custom aesthetics and custom quality to a broader range of clients in the past few years.
BREAKING OUT
No matter where these pools are being built, there’s been a recent explosion of creativity in vinyl-liner projects. In fact, we’re now seeing far more high-end clients opting for vinyl with the thought in mind that they can get more for themselves in the surrounding environment than they could otherwise. This has led to a diminution of the sense that these pools are somehow “inferior” to concrete vessels.
It’s come so far that I’d estimate that only 25 percent of our prospective clients harbor the old idea that ours is not only a less expensive but also a far more limited option. It’s actually great fun to disabuse these people of that notion by showing them our portfolio, which is now filled with projects that are hard to distinguish visually from gunite or shotcrete installations. Across the boards, the expansion of design options enables us to generate more excitement about what we’ve done, and it has completely transformed the way we talk about our work with new contacts.
Years ago, it was common to encounter new clients who would show us photographs of things they wanted in their pools. All too often, I had the unhappy duty of telling them that many of the options they wanted simply weren’t available with vinyl pools. Today, however, that rarely happens. In fact, the only feature I can think of that we can’t match is the beach entry, simply because vinyl still requires an edge with a track. Even in those situations, however, we’re able to provide a modified step detail that comes very close to a beach entry in appearance and function.
Using the full potential of available technology, we approach the design task for our vinyl-liner pools, spas and waterfeatures with a fully custom attitude: We are limited only by imaginations in conforming to our clients’ wishes, the setting and the extent of the budget and respond by developing unique shapes, using great materials and creating outdoor environments that please the eye and feel as though they truly belong. |
The key, of course, is that vinyl liners can now be made in just about any shape and size. We provide exact, precise measurements and dimensions to our suppliers and they’re able to supply exactly what we need in rapid order – usually within three weeks but often more quickly than that. We’re also able to obtain vinyl with internal contours to cover steps, thereby eliminating the fiberglass units that stood out so prominently and giving us far greater latitude in developing highly detailed shapes for spas.
Although literally every aspect of vinyl pools has been dramatically improved in recent years, the basic, governing concept has remained relatively unchanged. For those who are unfamiliar with vinyl-liner pools and spas, they’ve always involved installation of a system of solid walls with a narrow track on top. That track has a groove into which we snap the “bead” of a liner that hangs over the walls and contours of the vessel’s interior.
Once installed the weight of the water presses the liner against the walls and the bottom, creating a smooth, uniform, finished surface.
WALL WORKS
There are two basic ways to build walls for vinyl-lined pools and spas: with manufactured forms and poured-in-place concrete or with galvanized steel or polymer wall systems. We’ve used both – and they work beautifully – but our current preference is for using the concrete system, which at this time offers greater structural strength and flexibility in the shapes we can achieve. (I’ll stick with that option for purposes of this discussion.)
Although the forms are manufactured, they are now available in a range of shapes and radii that can be combined to create an endless range of shapes. Our forms – three feet wide by four feet tall and made of aluminum – give us a smooth finish and can be ordered in straight sections or curves. By combining different radii and these narrow-width forms, we can create an endless range of shapes.
Some of our most engaging work carries vinyl-liner pools into the realm of naturalistic watershaping. True, the liner’s bead is a visual presence, but when we succeed in delivering this much visual interest and variety above and beyond the waterline, the irregularity soon fades from our clients’ field of view. |
The walls in these cases are poured-in-place concrete reinforced with rebar in the same way as gunite or shotcrete pools. The walls are eight to ten inches thick and are engineered to withstand most soil conditions.
On site, we over-excavate the pool and set the forms up as freestanding walls, then backfill the area behind the walls once the forms have been stripped. The bottoms we install are almost all made of sand, which creates a small amount of “give” in the surface that our clients say they like and also constitutes a major cost saving. The sand is tamped and trowel-finished to create a smooth uniform surface. (In some cases, particularly in situations with unusually high water tables, we’ll install an unreinforced concrete bottom that adds enough weight to counteract the hydrostatic pressure of the water surrounding the pool.)
Market Mysteries I’m not entirely sure why vinyl pools are so closely associated with the northeastern United States. True, there’s a concern that concrete structures are subject to failure in colder climate, but there have always been gunite and shotcrete pools in the northeast and, when properly installed and maintained, they do just fine. Or maybe it’s a cost thing and the fact that in our area vinyl-liner pools cost an average of 30 to 40 percent less than their gunite counterparts. But price-sensitive consumers certainly live beyond the northeast, so that doesn’t completely explain the regional phenomenon, either. In fact, we know that there are builders in some Sunbelt regions who manage to provide concrete pools at prices comparable to vinyl, and it’s no secret that those “bargains” also come with all sorts of quality concerns that dog inexpensive gunite structures. In that light, if price was the sole concern, vinyl should’ve caught on in a big way as cost-saving option coast to coast – something that hasn’t really happened. In our business, one of the main comments we hear is that our clients don’t like the way cementitious finishes feel on their feet. It’s no secret that in plaster or pebble-finished pools (especially those that aren’t particularly well maintained), people complain about scrapes and irritation from rough surfaces. But again, it’s laughable to think that people in the northeast have more sensitive feet than do people in other parts of the country, so this is no solution to the mystery. While nobody seems to know with certainty why vinyl has always had such a strong regional association, there’s no question it does and likely always will. These days, however, we do know that the affordability of vinyl, combined with its new-found design flexibility, leaves more money in clients’ budgets for added features – attached spas, vanishing edges, ancillary waterfeatures, quality decking, fine peripheral hardscape materials, outdoor kitches and more. Whatever the regional issues, new developments in vinyl-liner pools have given us much more latitude when it comes to creating fully integrated backyards – and that, in my book, is a good thing indeed. — M.T. |
A key distinction of these pools compared to gunite or shotcrete is that, where hydrostatic pressure can spell disaster for concrete vessels by floating them out of the ground when they’re drained under the wrong conditions, it’s not an issue with a vinyl-liner pool. It does make a huge mess, but the entire structure never floats, only the liner does, so reinstallation simply means evacuating the water and reinstalling the liner.
That doesn’t happen very often, but when it does, the homeowner is looking at the cost of a big clean up and minor repair job rather than complete reconstruction of the backyard.
As mentioned just above, the walls in all vinyl-liner pools are freestanding, which means that raising the edge of a pool above grade or working on a hillside with an exposed wall or even a vanishing-edge detail does not pose a separate engineering challenge. In other words, the structures are essentially independent of the surrounding earth (or the lack of it).
COVERING UP
Unless we’re installing a liner with a standard size and shape, we take our measurements for the liner size and shape after we’ve installed the forms. It’s a painstaking process that sometimes requires dozens of individual measurements – whatever it takes to give the liner supplier enough reference points to get the liner just right.
With that order placed, we’ll go ahead and finish the pool by setting the plumbing and electrical lines and installing the equipment pad – basically anything that’s left to do other than actually installing the liner.
We’ve had some of our greatest ‘customizing’ success in cases where we’ve incorporated high-end touches including sculpted spillways, deck jets and other fountain features into our visual compositions. This layering of elevations, coupled with the use of high-quality stone, the latest modern amenities and well-considered plantings, has enabled us to please our clients and raise the bar when it comes to vinyl-liner pool design in our marketplace. |
These liners are heavy affairs, available in thicknesses ranging from 20 to 30 mils. The thicker liners are somewhat more puncture resistant, but we found that 20-mil liners are sufficient for the vast majority of applications – that is, except in cases where the client lets us know that the pool is likely to see rough play or usage by pets, in which cases we encourage them to go with the thicker material.
A New Shape With the advent of liners that can fit over steps and benches, our firm has taken to building vinyl-liner spas attached to pools or as stand-alone systems. As described in the accompanying text, the increasing flexibility we’re seeing in pre-fabricated forms and poured-concrete structures has been augmented by advances in liner technology that have made them more durable in the face of chemical treatment, the corrosive effects of which can be magnified in spa systems. These developments have opened up discussions with clients about how they use their spas, and in these conversations we’ve found a growing number of people who want a body of water that enables them both to exercise and enjoy the relaxing benefits of hydrotherapy. To accommodate those needs, we’ve developed a hybrid vessel we call a “spool”: It’s either an oversized spa or a smaller-scale swimming pool with hydrotherapy jets, and all of them seem to be landing in the 15-by-20 foot size neighborhood. In many cases, our spools have one end that’s five- to five-and-a-half-feet deep, which enables our clients to stand up and engage in water exercises. In other systems, we’ve installed swim-jets that enable clients to swim in place. With this sort of multi-faceted functionality, these vessels offer a great deal of enjoyment and healthful use at a cost that would be hard to approach in gunite or shotcrete. — M.T. |
When punctures do occur, the kits used to patch holes nowadays enable repair technicians to make patches that are as strong as the original material and blend in seamlessly with the appearance. Moreover, liners have come a long way with respect to resistance both to ultraviolet radiation and harsh chemicals.
With all that durability, it’s common to see liners last upwards of 15 years, which is certainly comparable to plaster or pebble finishes. In fact, only tile surfaces – which last indefinitely but cost ten times or more what a liner does – are more durable.
There’s a nice flexibility factor, too: We’ve run into clients who will change their liners simply because they want a different look. And no matter whether they’re changing it because it’s worn out or just because they crave a fresh look, replacing a liner is a simple and affordable process – certainly much less involved, costly and messy than is refinishing a cementitious finish.
Liners are installed as they always have been, simply by unpacking and unfolding the sheet in the pool bottom and snapping its “bead” into a track. In most cases, we protect the sand bottoms of our vessels from indentations by working from the top.
GOING CUSTOM
With the new complexity that attends some of our work – including waterfalls, grottos and rockwork edges – we’ve seen the need to get creative in our approaches to hanging liners while protecting the pool’s floor. In some cases, for instance, we’ve had to hang an installer over the edge by his feet to snap the liner into place. But even in the most complex and sizable of installations, the process of installing a liner seldom takes more than a few hours.
There is a bit of stretching involved, of course, which helps us achieve a tight fit over the internal contours of the pool or spa. How far a liner will stretch is dependent upon the temperature at time of installation. This is why manufacturers now provide “summer” or “winter” cuts for their liners, with the winter sizing being a few fractions of an inch larger because the material will not be as flexible when it’s cold.
Prints and Patterns Back when vinyl liners were new, there wasn’t much to choose from by way of appearance. Not only did they come in a limited array of sizes, but the first liners I saw 30-plus years ago were all blue – and pretty much the same shade of blue at that. Those products were essentially retail items that were available as boxes sitting on shelves, and it’s been fascinating through the years to watch the situation change. The next step after the blue was a variety of pebble patterns, and for a while that’s what almost everyone used. This development opened the door, and a much wider array of patterns and colors began to emerge, from speckles, pebbles and geometric patterns to aquatic scenes and tile reproduction. There are now almost too many choices, so much so that clients have a hard time deciding what they want. The colors manufacturers are now using don’t exactly align with colored plaster or pebbles, but they do provide roughly the same sets of options when it comes to teals, earth tones and grays. There are also extremely dark colors that enable us to create “black-bottomed” pools and spas, and there are some liners that have reflective white highlights that make them shimmer underwater. Looks come and go, of course, and it’s possible for some of us who’ve been at it for a while to judge a pool’s age by its liner. For a time, printed faux tile bands at the waterline were extremely popular, for instance, but those days seem to have passed. What’s great about the current market situation is that manufacturers are becoming more sophisticated and responsive in developing the colors and patterns they offer. When you combine vinyl options with advancements in shapes and contours, these pools and spas are becoming increasingly “custom” in every sense of the word. — M.T. |
Penetration in the liners for suction and return lines, skimmers, lights and hydrotherapy jets are sealed using mechanical gasket systems that essentially sandwich the liner in a compressed, water-tight fitting. There’s no adhesive involved, so that when a liner is replaced, it’s simply a matter of removing the fittings and reusing them. As with all other aspects of liners, these gaskets have come a long way, and we virtually never have problems with leaks.
Indeed, manufacturers of liners and wall systems have all seen the benefits of working in custom shapes, and in just about all cases we’ve found tremendous flexibility and willingness on their part to try new things in ways that make the entire process both innovative and exciting.
The best thing about this progress is that companies like ours – that is, companies that see value in being able to deliver clients exactly what they want and in bringing a true spirit of creativity to the process – are now working as members of teams that include architects, landscape architects and other design professionals. We’re called on to answer questions about what we can achieve using liners and often make aesthetic recommendations about greater design schemes.
From start to finish, we’re finding that the words “custom” and “vinyl liners” are no longer mutually exclusive. We feel we’ve joined the greater watershaping world in terms of providing products that are closely suited to client needs and personalities as well as the requirements of the overall setting.
It’s been a long time coming, but these steps up in quality and aesthetic potential will surely define our future as members of the watershaping industry.
Michael Truehart is owner and founder of Northport, N.Y.-based True Blue Pools, a firm focused entirely on the design and installation of high-end, custom vinyl-liner swimming pools and spas. He began his career in high school, working part-time as a pool installer. Following undergraduate work at Suffolk Community College and Albany State University in economics, he focused on the swimming pool and spa industry and has been part of it ever since, pursuing projects throughout the state. His firm specializes in executing high-end construction processes in ways that are unobtrusive and pleasant for its clients.