Portland Limestone Cement (an impactful change)
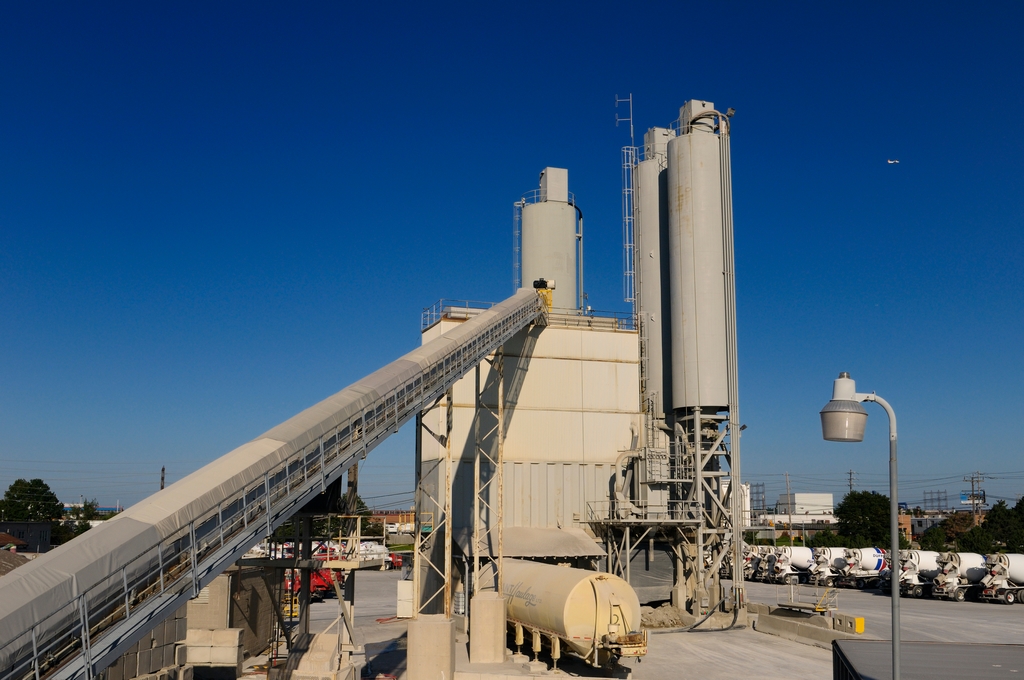
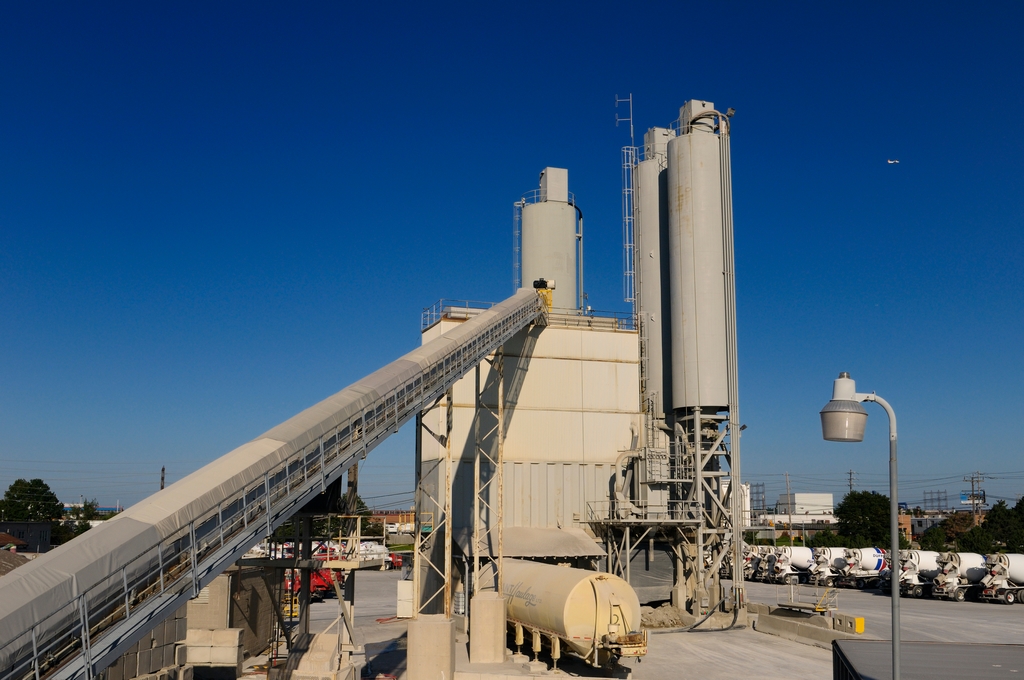
The introduction of Portland Limestone Cement (PLC) is intended to dramatically reduce the carbon footprint of concrete production. That good intention may, however, come with unintended consequences, says plaster expert and educator, Jon Temple.
By Jon Temple
Sometimes even seemingly good ideas have unintended consequences. I strongly suspect that might be the case with the advent of Portland Limestone Cement.
In case you’re not aware, this material is being widely introduced as a carbon-reducing alternative to traditional Portland Cement. While well-intended, based on my decades of experience working with Portland Cement in my pool plastering business, my hunch is the impact will be widespread and, in some respects, lead to confusion and possible negative outcomes.
First, let’s look at the big picture for context. Other than water, concrete is the most-used material on the planet, representing about 50% of all manmade materials by mass. Because we use so much concrete each year, even small changes to its formulation can have dramatic effects on the construction industry’s annual carbon footprint, thus benefiting everyone on the planet.
Those changes can also have a direct and widespread impact on formulations, mix schedules, packaging and application methods.
WHAT IT IS
To be sure, the arguments in favor of PLC can be compelling. For instance, if all cement used in the U.S. in 2019 had been converted to PLC (Type IL), it would have reduced CO2 emissions by 8.1 million metric tons, which the U.S. EPA says is the equivalent of taking 1.75 million cars off the road for an entire year.
The construction industry at large has recognized that they can play a big role and continue to innovate for better binders with even more favorable environmental performance. PLC has been extensively tested, some say proven, and it is now readily available through the same existing supply chain.
Sustainability encompasses many aspects designed to improve construction practices, including: more efficient use of natural resources, better thermal performance of structures, and reduced environmental impacts, with a focus on embodied carbon.
Like all building materials, Portland Cement has an environmental footprint, and it’s often described in terms of greenhouse gas (GHG) equivalents. Cement is made by grinding clinker—the main energy intensive ingredient—to a fine powder. Producers know that replacing some of the clinker in Portland Cement with ground limestone offers benefits, the most important being that it reduces the embodied CO2 of the cement.
Portland Limestone Cement (PLC) is a blended cement with a higher limestone content, which results in a product that works the same, measures the same, and performs the same, but with a reduction in carbon footprint of 10% on average. At least that’s the big idea.
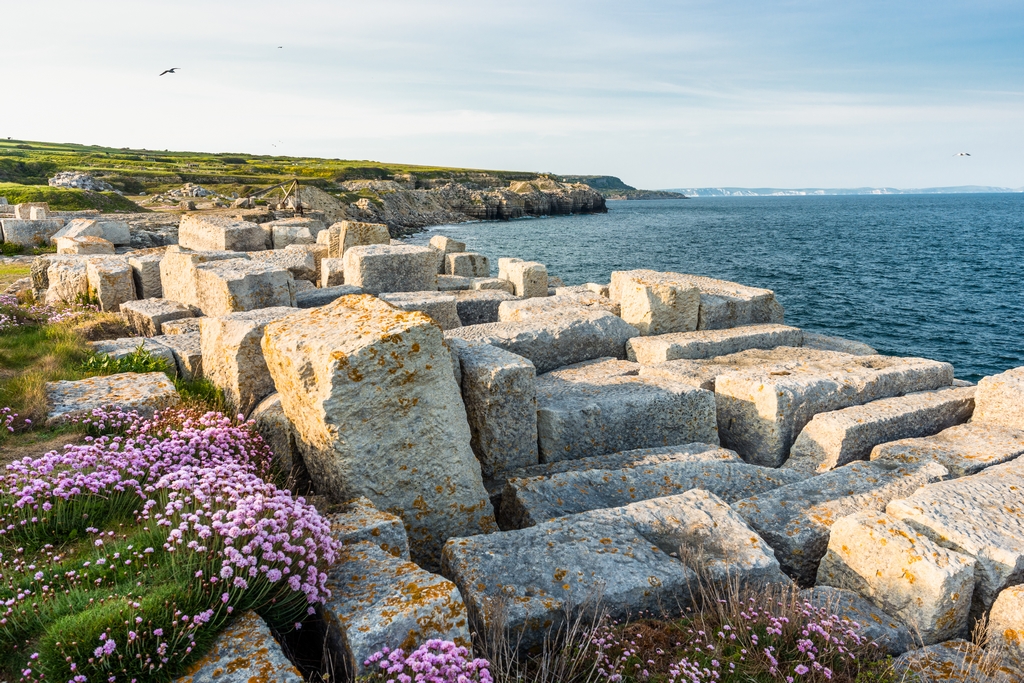
The U.S. standard for Ordinary Portland Cement (OPC) allows for up to 5% of clinker to be replaced by limestone, the standard for blended cement allows for 5% to 15% limestone replacement in PLC (Type IL). Concrete mixes designed with PLCs are compatible with all supplementary cementing materials (SCMs).
The claim is that you can continue to use all the other materials you use to make concrete for an even greater reduction in carbon footprint.
SIGIFICANT CONCERNS
Assuming for the sake of discussion that PLC offers environmental benefits as advertised, it also presents certain possible disadvantages that warrant serious consideration. Simply saying that it works exactly the same is a blanket assumption that can, and I believe will, lead to trouble.
When surveying academic papers on the subject, you’ll quickly find a number of potential PLC pitfalls. As one example, according to Lachana Poudyal, et al, in Mechanical and Durability Properties of Portland Limestone Cement (PLC) Incorporated with Nano Calcium Carbonate (CaCO3), “Despite lower environmental impacts, the use of Portland Limestone Cement (PLC) concrete has been limited due to its reduced later age strength and compromised durability properties.”
One of the primary concerns with PLC is its potential to reduce the early strength of concrete compared to OPC. The replacement of clinker with limestone can lead to slower hydration rates and, consequently, slower early-age strength development. This can be a critical factor in applications where rapid setting and early strength gain are essential.
The incorporation of limestone can alter the setting time of the cement paste. In some instances, PLC might exhibit longer setting times compared to OPC. Delays in setting can impact construction schedules and may necessitate adjustments in concrete mix designs or the use of setting accelerators.
While PLC can enhance certain durability properties due to the pozzolanic reaction of limestone, excessive limestone replacement levels might compromise long-term durability. High limestone content can lead to increased porosity and reduced resistance to aggressive chemical environments, such as sulfates or acids.
When they are grinding the limestone and the clinker together, the limestone is a lot softer, so it’s going to turn into more of a powder. When you start getting your sizes differently, you get dry times differently.
Although PLC can mitigate alkali silica reaction (ASR) concerns due to reduced alkali content, it does not eliminate the risk entirely. In certain conditions, the presence of limestone can contribute to ASR, leading to expansion and cracking of concrete structures over time.
NOT SO COLOR-FAST
The use of PLC can result in variations in the color of finished concrete. Limestone typically has a lighter color than clinker, which might affect the aesthetic appeal of concrete structures, especially when color consistency is desired.
In simple terms, the limestone filler is not going to grab the dye. So, you have to, in effect, glue it to the cement with a binder. So, you take an 18,000-gallon swimming pool, that’s about 450 surface square feet, including walls and floor, square footage. To plaster that pool, if you put the binder in it and you bought it separately, is around $500 to $600.
The problem really comes into play with some pre-mix manufacturers who claim that no binder is needed to create a color-fast finish. If there’s one takeaway from this discussion, it’s be sure to know the mix design of the product you’re using.
TO GOOD USE
PLC has been tested over the last few years with different additives but those results have not been broadcast to our industry. I believe the premixed companies are further along than the job site mixes because it’s more of a warranty responsibility with premixed. I personally do not think the cement industry, or most pool associations, have educated our industry enough.
At our company, Tempool, along with our vendor partners, Federal Cement and CL Industries, we have been testing PLC for the last year, have been using a lot of it on a regular basis, and are having great success – but it’s far from a simple one-to-one replacement. The bottom line is we still have much to learn about the use of PLC as an industry.
We can reasonably conclude that proper mix design, quality control, and thorough understanding of its limitations are essential when incorporating PLC into construction projects.
Jon Temple is president and founder of Tempool, a pool-surfacing firm located in Jacksonville, FL. Temple founded the company in 1996, which has plastered more than 30,000 pools. He is a valued Watershape University faculty member.
Opening image: Long crushed limestone conveyer belt at a Toronto cement factory Toronto, Ontario, Canada. Photo by Reimar | Shutterstock