Keeping Watch
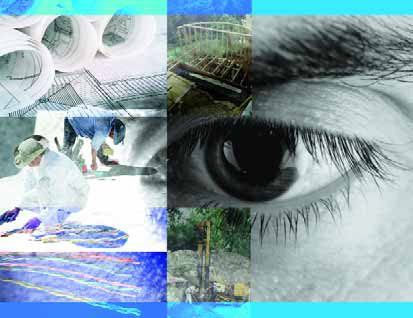
I’m always amazed when I hear other watershapers complain about inspectors.
As I see it, those professionals provide a valuable, extra set of eyes on site – eyes with an expertise that helps me make certain a project is being installed as engineered and specified. In essence, inspectors are a sort of insurance policy against problems both at the time of the inspection and down the line.
In the last several “Details,” we’ve systematically followed the design and construction process and, last month, discussed the installation of steel and plumbing in anticipation of the arrival of
the shotcrete or gunite crew.
Whether it’s required by the local jurisdiction or not, I always invite a deputy inspector to be on hand for the shoot to watch what happens relative to the engineering plans and observe basic issues of workmanship. I do so because the shoot is an absolutely critical project stage – our last chance to make adjustments and corrections that can ensure the long-term structural integrity of a watershape’s shell.
I’m there to meet the inspector first thing in the morning, and I don’t leave the job site until every bit of steel is covered and every detail addressed, from cutting notches for overflows to making absolutely certain there are no broken pipes.
To provide all of us with a clearer sense of what inspectors do and how they do it, I’ve invited Richard Fehring, a licensed and registered deputy inspector for the city and county of Los Angeles, to write the rest of this month’s column. It’s an eye-opening discussion – one that defines in ways I never could the importance of what inspectors do in support of watershaping.
— D.T.
As a deputy inspector for the County of Los Angeles, I see my job as one of protecting a project engineer’s work as well as the interests of the contractor and the homeowner.
I’m there to make sure that all the work I’m inspecting is done to code and that the pool or other watershape structure has structural integrity. Some people tell me I have the easiest job in the world, because much of the time it looks like I’m just standing around. Yes, I do tend to keep a low profile on a job site, but every second I’m there, I’m carefully observing a host of significant details.
When I notice something and bring up a problem, I’m aware that this can be frustrating for a contractor and that some degree of irritation on his or her part is a normal reaction. But what I’m catching are mistakes that need to be corrected; otherwise, my aim is to be unobtrusive and stay out of the way.
Generally – and despite the fact some contractors have a tendency to question what I do – my desire on the job site is to be helpful, supportive and constructive.
LONG DAYS
On the day of a shoot, I generally arrive on site a bit early – usually 30 to 45 minutes before anyone else comes on the scene.
The first thing I do is make sure the contractor has left the appropriate permit in the permit pouch, ascertain that the city inspector has been there and signed off on everything to that stage and determine if, in legal terms, the pool is ready to shoot. If the paperwork’s in order, I’ll walk around the pool and recheck everything – grades, rebar sizes, clearances and any of a number of other details that catch my eye.
I always examine the steel, for example, making certain first of all that it’s been installed per the structural plans. If the city inspector has signed off on it, I know that it was very likely correct at the time of the inspection, but sometimes things happen between the time he or she leaves and I get there. One common problem: Quite often, there’s no longer adequate clearance between the steel and the dirt, in which case I’ll ask the contractor to insert more spacers or dobies to re-establish spacing that will ensure proper encasing of the steel in the shotcrete.
I arrive on site on the day a pool or other watershape is to be shot a good 30 to 45 minutes before anyone else. My first task is making certain all of the project paperwork is in order and the watershape is legally ready to go. |
I then check to make sure that all of the steel and any other metal components are properly grounded with UL-approved clamps. City inspectors are not infallible: They do occasionally miss important details such as this, and it’s my responsibility to rectify the problem. This of obvious importance, as nobody wants to see anyone get electrocuted when they jump in the water!
Next, I’ll visit the equipment pad and check the plumbing pressure on the gauge, making certain it stands at about 35 to 40 pounds per square inch in every case. I’ll make a note of these readings so that later on, during the shoot, I can recheck to make certain the pressure stays the same. If there are fluctuations, it typically means there’s a leak somewhere – a rare event, but one I watch for nonetheless.
Finally, I check to ensure that the site is physically ready for the shoot, with clean rebar, no debris and no stray parts lying around. This is important, because a lot happens on site between the city inspection and the shoot. Plumbers, for example, sometimes cause a good bit of dirt to slough off walls in laying and securing pipes – an occurrence that can compromise clearances.
If small issues such as these aren’t addressed before the shotcrete crew shows up, it means they’ll have to stop and police the site themselves – a waste of valuable time and money. Worse, if no one takes care of this last-minute cleanup, then the pool shell won’t be properly installed and there could be structural problems down the road.
PROPER SUPERVISION
Therein stands a key point: Not only is it important that I show up early to run through this set of details, but it’s also vital for the contractor to have someone on site to deal with these sorts of issues when I raise them.
Dealing with my observations is critical enough, but what happens without this level of on-site supervision is that key decisions are left to the shotcrete crew. For instance, there are almost always questions about step detailing and any number of other basic dimensional issues: If a responsible party isn’t on hand, the entire process slows down and can even come to a complete halt.
As I see it, the shotcrete subcontractor should never be left to make what are, after all, real design decisions. Principles of sound project management require the contractor to be capably represented on site when a watershape shell is shot, but unfortunately that doesn’t always happen – and substantial problems are often the result.
Before the shoot begins, I also examine the physical layout of the watershape, making certain the steel has been set up according to plan and checking to ensure that there’s adequate clearance between the steel and the dirt to allow the crew to encase the steel properly. |
In even more pointed terms, it’s not the shotcrete subcontractor’s responsibility (or mine) to serve as an intermediary with the client. Homeowners often have questions while the pool is being shot: The subcontractor is mostly too busy to answer them – and so am I – at a time when there may be need for significant communication.
And on those occasions when I see a problem that needs to be addressed – say if an extra piece of steel is needed in a step or in a dam wall – I’m not going to raise the issue with the shotcrete subcontractor or his crew: Instead, I need to speak with the contractor, and having someone on site facilitates an immediate response to issues that can eat up time and money.
It’s always been my contention that the contractor (whether it’s a general contractor, a pool contractor or an owner/contractor) needs to ride herd on the job site and make certain that each sub-trade does its bit to maintain a clear, clean job site. It’s been my observation that, when things go wrong, problems will tend to snowball and bury any profit a job might yield.
This is why contractors need to take care in selecting subcontractors. It’s also why I’m such a strong advocate of having project meetings before a job starts so that everybody who will be working on the project’s construction team knows exactly what’s expected.
The proof really is in the pudding: Within a few minutes of being on site, I can tell if crews are good because of the way the fundamentals have been handled.
MAKING WAY
By the same token, there are occasions when things are obviously wrong and need to be addressed before any shotcrete is applied.
Proper form elevations, for example, can become a big issue. All too often, a shotcrete crew will show up to find a pool out of square and with incorrect elevations. These are not issues they should need to address upon arrival on site: Dealing with them involves delays and results in a mixer truck that shows up at 7:30 am sharp sitting there for a costly hour or two before shotcrete application can begin.
After making certain the mix design is the one specified for the job at hand, I observe the shoot and keep a watchful eye on the nozzle: I’m always on the lookout for good coverage of the steel, the angle at which material is being applied and the pattern in which the nozzle operator applies it. |
Basic site access is another issue that is too often overlooked until the day of the shoot. It’s common to find cars in the way of mixer trucks and pumping rigs – something that should have been addressed by the contractor well ahead of time with the homeowners and their neighbors.
If there’s no room in the driveway and limitations in street access makes it tough for mixer trucks to come and go, the hassles multiply and the day fills with frustration. And it has rippling effects, upsetting the homeowners and their neighbors as the contractor does whatever it takes to clear the way. The issues may be easy to address, but dealing with them consumes both time and money.
Preferences It’s not my place to dictate what materials are used on any given watershaping project, but as I mentioned in the accompanying text, I prefer working on projects having shells made with shotcrete rather than those done with gunite. After inspecting more projects than I care to count through the years, I’ve come to appreciate the significant differences between these two types of pneumatically placed material – and I must give shotcrete the edge. So what’s the difference? Technically speaking: [ ] Shotcrete is made by way of an engineered mix designed at a batch plant. It’s precise, comes ready-to-apply in the truck and is extremely consistent in its content of cement, sand and aggregate. As the name implies, it’s pneumatically shot into place. [ ] Gunite requires a far more complex on-site operation in which loads of sand and cement are skip-loaded into a huge mixing machine that looks like a calliope and spews diesel fumes. It’s messy to start with, and if there’s any wind at all, the material will migrate all over the street, the clients’ yard and neighboring properties.As I see it, the advantage of shotcrete is that there’s less room for error. With gunite, you have one person controlling the mix and another working the nozzle controls, and both can jumble things with ease. In more direct terms, gunite jobs are so complicated that they require two inspectors, one back at the gunite machine watching the mix, the other watching the nozzleman as he (and it’s almost invariably a man) controls levers for air, water and the material – and that control must be precise. By contrast, shotcrete has a control for air, and there’s no way to foul up the mix. Many operations effectively install pools using gunite, but in my view, it’s simply more of a challenge than it should be. — R.F. |
When the shotcrete crew shows up, my first job with them is to check the mix design and make certain the right batch has been delivered to the right address. Again, this is an extremely basic thing, but it can be a huge problem when things go wrong. I’m also aware of the operational distinctions between gunite and shotcrete, and my preference has always been projects that involve the latter. (For more on this, see the sidebar at right.)
Once the crew is set up and we’re sure everything is as it should be, the application process begins and I become an attentive observer. My main concern is the nozzle: It should be held approximately perpendicular to the surface and never at any angle greater than 45 degrees off the perpendicular because that tends to create a sort of folding action in the shotcrete that traps rebound. There are, of course, certain situations in which access around complex details is an issue and there’s no other way to shoot portions of a shell other than by holding the nozzle at an off angle, but as a rule that’s not an acceptable application technique.
I’m also looking to be sure the nozzle is being moved correctly, typically in a series of small circular motions. If the nozzle is waved too quickly, it changes the angle of impact, increases overspray and leaves a rough texture on the finish work. I’m also always looking to make sure there’s good overall coverage – at least three inches over the steel with good compaction with the material.
As the day progresses, I’ll continue to check mix designs as new trucks show up and generally do what I can to make the process unfold smoothly.
END OF THE DAY
When the work is done, I write a report for the pool contractor and the city inspector that carefully details any problems I’ve seen and corrective measures taken. If everything’s been done correctly, these reports are short, but usually I find a couple points worth discussing, large or small.
As a final on-site step, I make sure the contractor has provided for keeping the shotcrete wet, whether it’s through having the homeowners do it, setting up a system of drip hoses or assigning someone to return to the site to take care of things.
None of this process, end to end, should be unfamiliar to contractors, all of whom should be well versed in the American Concrete Institute’s standards for pneumatically applied concrete (ACI 506-R 95). This document defines all aspects of shotcrete installation for swimming pools, including workmanship, mix designs and strength.
If you follow those guidelines and take care of the basic concerns I’ve described here, your projects stand a fair chance of making it through the shoot without a hitch.
— Richard Fehring
Richard Fehring is a license and registered deputy inspector for the City and County of Los Angeles.
David Tisherman is the principal in two design/construction firms: David Tisherman’s Visuals of Manhattan Beach, Calif., and Liquid Design of Cherry Hill, N.J. He can be reached at [email protected]. He is also an instructor for Artistic Resources & Training (ART); for information on ART’s classes, visit www.theartofwater.com.